
Industry
Agriculture
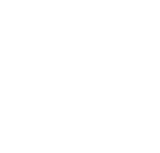
Challenge
Accuracy
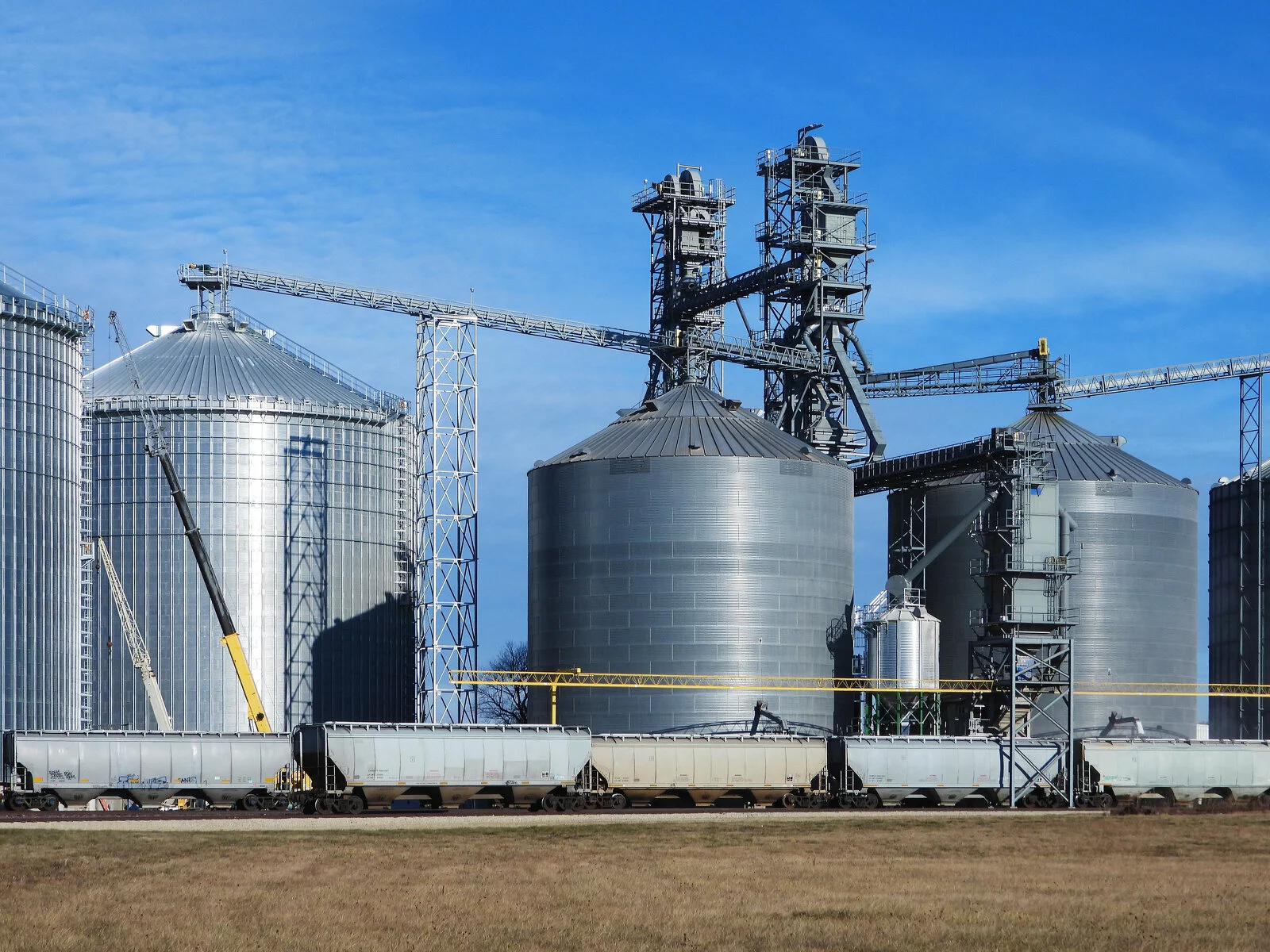
Challenges
Aligning three separate flanges accurately is hard enough. For this manufacturer of pit hoppers, the task was complicated by the fact that some of the flanges were rotated at an angle, making it difficult to measure. Plus, the hopper has to fit seamlessly atop a grain leg 120-180’ up in the air. Ensuring that the holes lined up was crucial – even a slight misalignment of 1/16” at the flange could add up to inches off at final assembly.
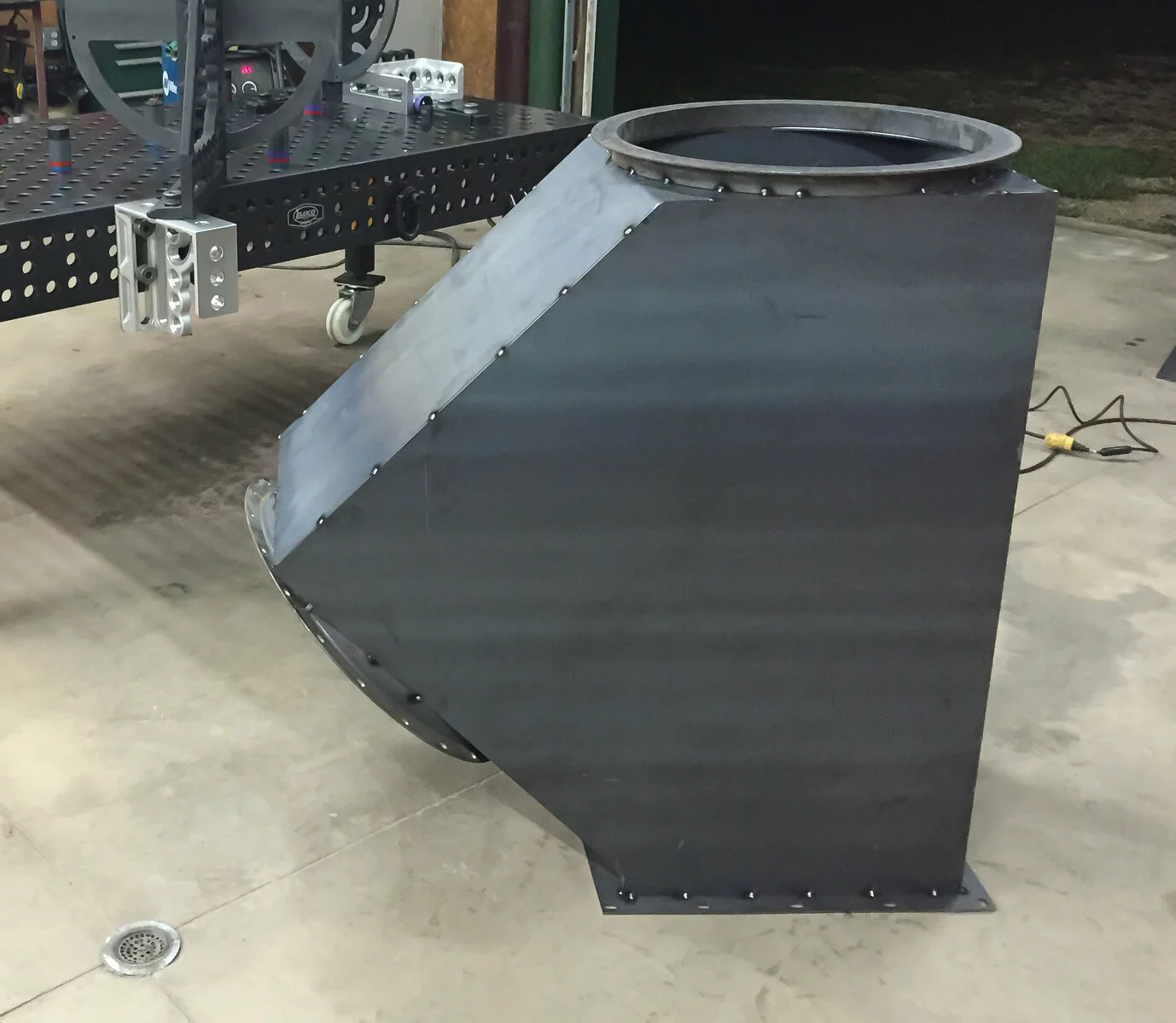
Solution
• 3D Welding table with large angles
• Custom adapter
Flat plates are positioned so the center of the flanges falls in the center of the fixturing angle. This ensures that each opening is set at the same plane. The custom adapter lines up with the holes in the flanges, and rotates around the center of the flange. This provides the flexibility needed for accurate alignment, regardless of the angle.
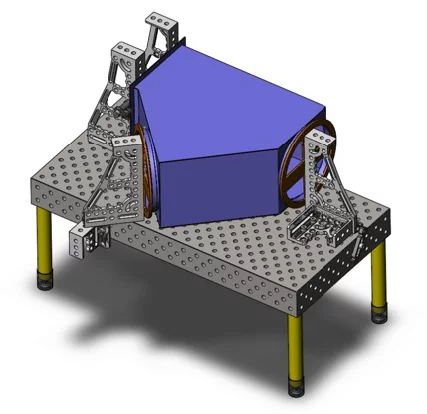
Result
The centerline alignment of the flanges is now instantly achieved and fully repeatable, eliminating the compounding errors that complicated assembly, or led to rework.
The spot-on accuracy of the hoppers made with the new modular solution couldn’t be any clearer than when the millwright assembling the grain leg called to ask “What did you change?” All of the difficulties he’d had before with the hoppers were gone. The customer’s answer: “We called Bluco.” Being able to collaborate with experienced engineers who understood their challenges ultimately led to a modular solution that removed roadblocks and enabled success.
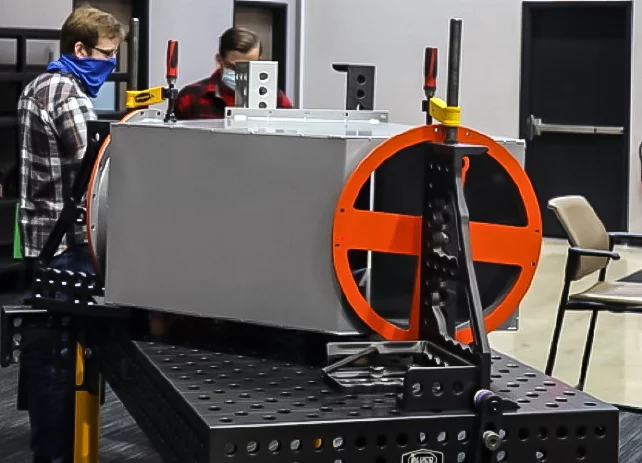

New: Bluprint™
Proposals only show how much it will cost. BluPrint proves how much you can gain.