Dedicated Vs. Modular: Rethinking the Decision For Today’s Manufacturing Reality
Weighing the benefits of dedicated vs. modular fixturing systems to stay competitive and efficient.
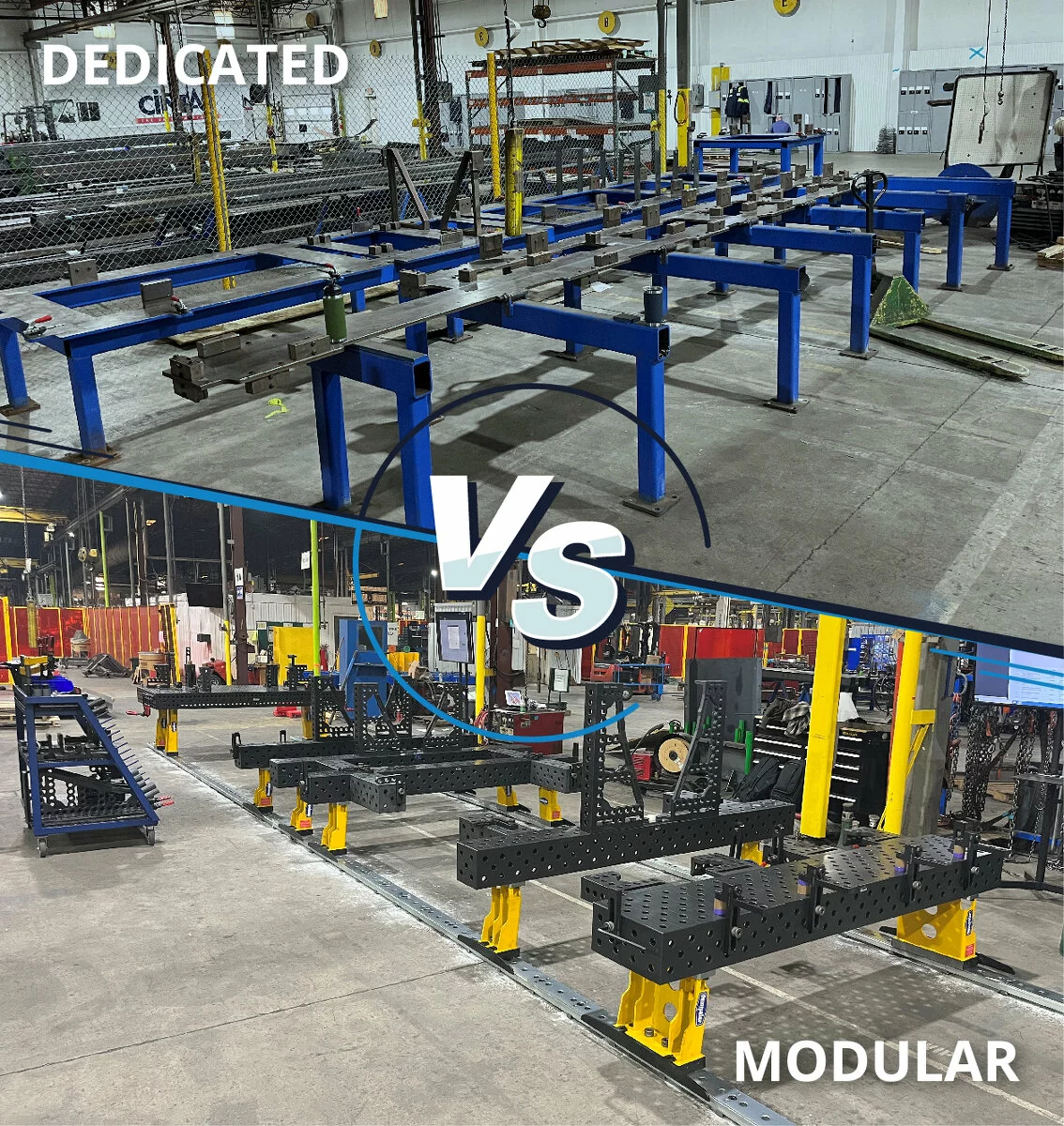
Navigating the manufacturing industry is a bit like sailing a boat in open water. To the captain focused on daily duties, small shifts in wind and tide barely register. However, over time, these subtle changes can alter your course completely.
Similarly, while day-to-day changes in manufacturing may seem like business as usual, the cumulative effects build up. A combination of evolving consumer demands, advancements in technology, and changes in both supply chain and workforce dynamics have slowly but profoundly reshaped the landscape.
As a result, the way we make decisions about the production process also has to change. This is especially true when it comes to workholding. The choice between dedicated vs modular fixturing now involves a new set of considerations. If you currently have a mix of modular and dedicated fixtures, or if you’ve always thought certain applications were better suited for dedicated fixtures, it’s time to re-calibrate in order to stay on course.
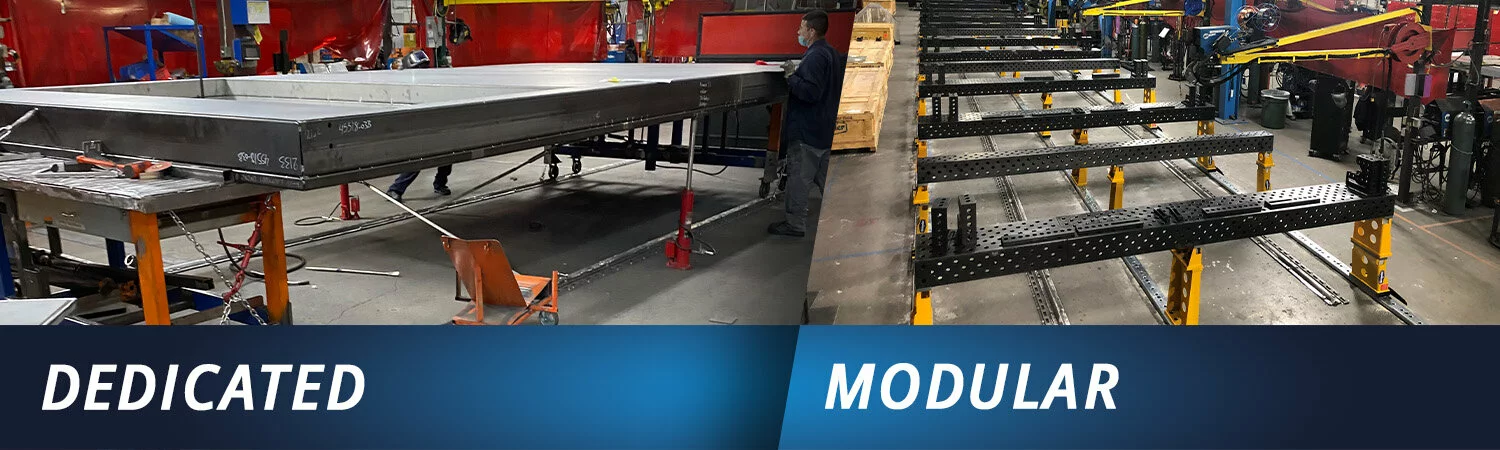
Modular fixturing: Designed for today’s custom manufacturing needs
A hundred years ago, mass production made its debut. Over time, customized manufacturing became a small niche. But for decades, the more common goal was standardization. The idea was to minimize variation in the end product and in the production process.
When workholding eventually became commonplace, dedicated fixtures were a great fit for mass production. Sure, they take a long time to make, and only do one thing. But back then, manufacturers had more time to spare and fewer product variations to contend with. Their lack of flexibility was outweighed by their ability to churn out products with minimal adjustment and high accuracy.
Fast forward to 2024, when changing customer expectations have made customization much more than a niche. In fact, custom manufacturing is growing faster than ever before. According to one study, the global custom manufacturing market is predicted to grow 57.2% by 2031 [1]. With increases like these, an OEM manufacturer’s ability to offer customization is vital. It’s a value-add service that opens the door to new business and higher profits.
But custom manufacturing strategies (which include ETO/Engineered to Order, BTO/Built to Order and HMLV/High Mix Low Volume) require something that dedicated tooling wasn’t intended to provide: versatility.
Enter, modular workholding systems. Versatility is where modular systems shine. The ability to change, modify and utilize modular components across multiple parts, product lines and production cells makes it easier to setup and changeover to adapt for each custom part. Modularity reduces downtime and improves efficiency without sacrificing precision.
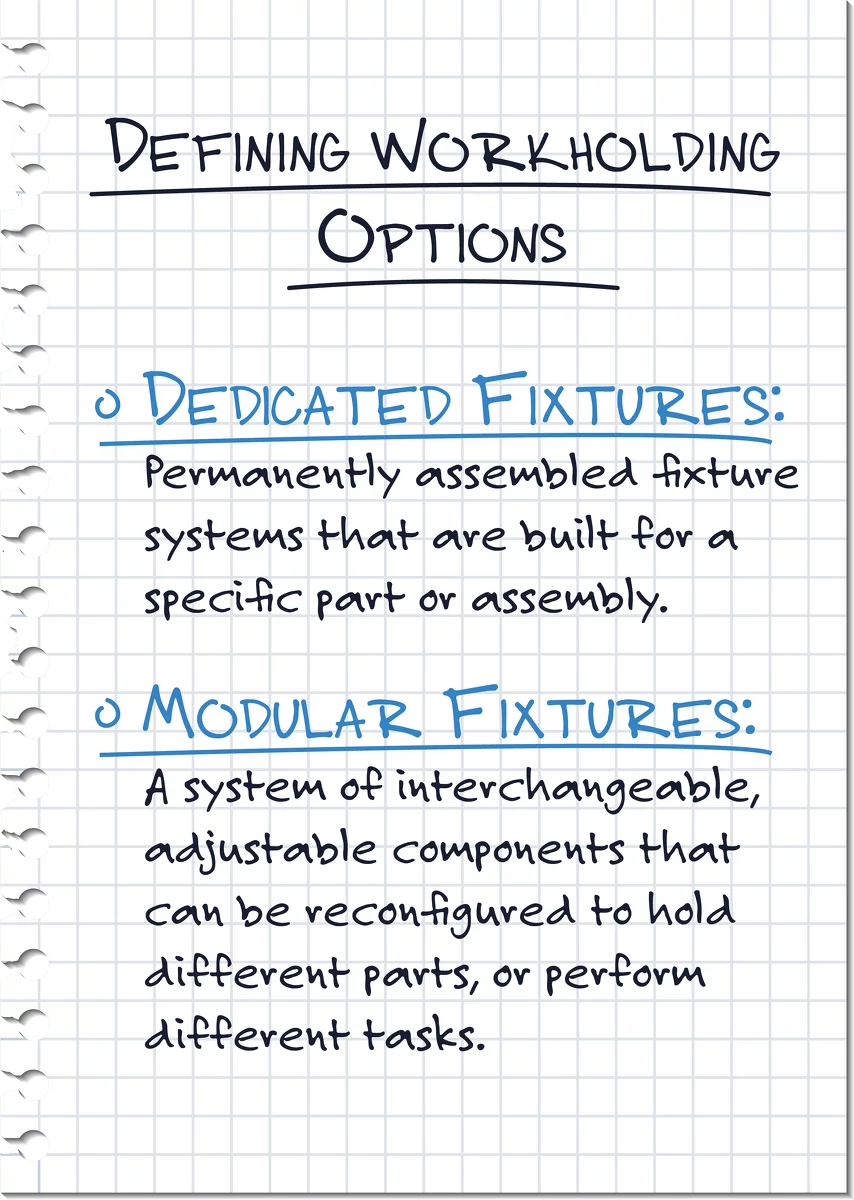
Why modular fixtures are built for evolving technology
The rise of customization was helped along by advancements like AI, IoT (the Internet of Things) and automation. These technologies not only make the ETO/BTO model easier to manage, they’re also changing how manufacturers approach dedicated vs modular fixturing.
In the past, the reliability of a dedicated fixture provided peace of mind, despite any drawbacks. However, in today’s fast-paced technological landscape, there’s a real risk that the system could become outdated before it’s even fully installed. At best, upgrading a dedicated fixture involves significant and costly reengineering. At worst, it becomes obsolete.
Here again, the versatility of modular systems offers some big advantages. Modularity allows manufacturers to stay at the cutting edge of technological advancements, no matter how fast they develop.
Looking specifically at automation, there are a lot of new factors to take into account. While custom manufacturing processes require versatility, the integration of robots and cobots into that process means that precision and repeatability are also vital. Modular solutions tick all those boxes, while dedicated fixtures often fall short.
For manufacturers transitioning to automation, the adaptability of modular solutions can also help bridge the gap between old and new production methods. With a little engineering forethought, a single modular solution can transition from a manual process to a fully automated robotic cell with minimal reconfiguration. Instead of two dedicated solutions (one of which will likely end up out of service) a single modular fixture is often the more sensible solution when deciding between a dedicated vs modular fixture.
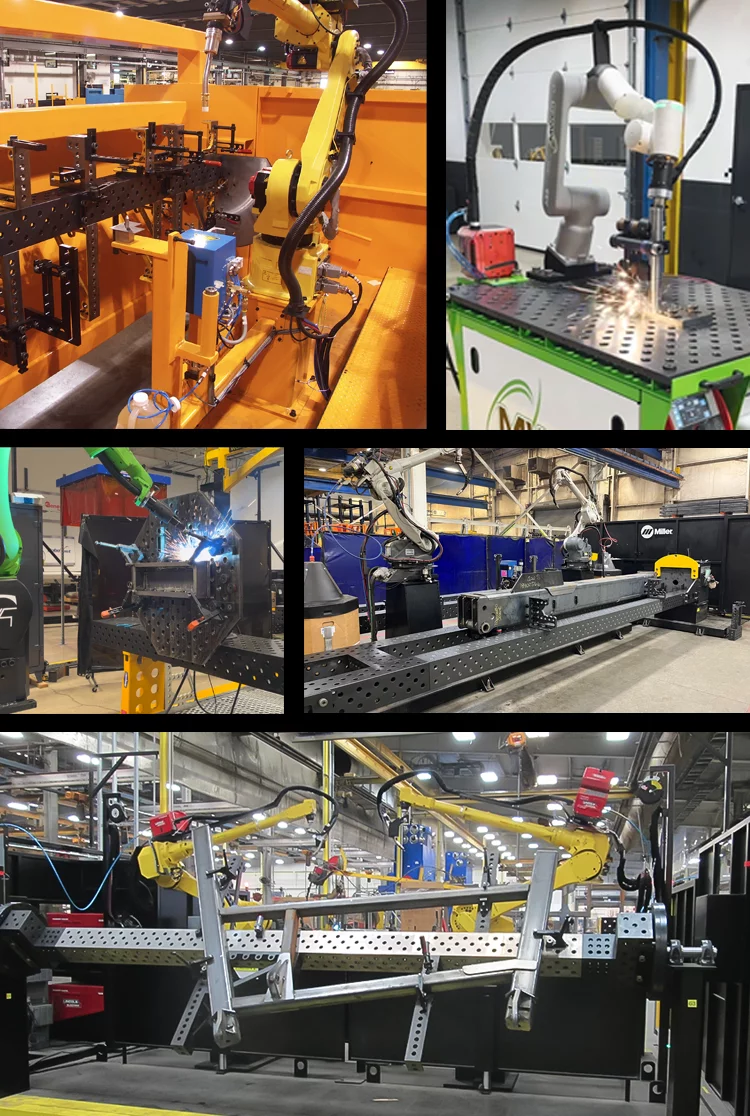
Want help comparing options for an automation project? Explore BluPrint™ — our guided process for smarter fixturing.
How modular workholding supports supply chain agility
When we think about current supply chain dynamics, “consistency” and “reliability” are not usually the first words that come to mind. In fact, today’s supply chain often looks a little rusty compared to the long, strong chain of decades past.
Back in the day, manufacturers could rely on a steady flow of materials with minimal disruption. They had long-term contracts and established relationships with a small set of suppliers who could provide the same thing every time. In other words, consistency was king. And global sourcing was queen.
Manufacturers prioritized low cost over location when it came to sourcing raw materials. But optimizing a supply chain based on efficiency and cost often came at the expense of flexibility.
Today, priorities have shifted. While consistency was king in the past, risk mitigation de-throned yesterday’s priority. In a world where supply chain disruptions are not only commonplace, but more frequent and longer lasting, there is nothing more important than the power to pivot.
Manufacturers now look to diversify their supplier relationships, so that if one can’t deliver, another can. And instead of global sourcing that prioritized cost of materials, we’re more focused on taking control of the timeline. For that reason, reshoring, nearshoring and even bringing projects in-house make much more sense today.
All of these changes add up to yet another reason to re-evaluate whether to choose a dedicated vs modular fixture. Yesterday’s reality (a small number of suppliers providing consistent parts on a reliable schedule) was well-suited to workholding designed to hold one part for a long time. Today’s reality (multiple suppliers that provide variable parts on uncertain schedules) is better suited to a workholding system that can quickly and easily adapt to varying parts and new processes.
The versatility of modular systems provides the resilience and agility needed to accommodate changes in supply chain dynamics without significant downtime. They offer a level of flexibility that dedicated fixtures often can’t match. The result? Manufacturers can pivot more easily in response to unexpected challenges.
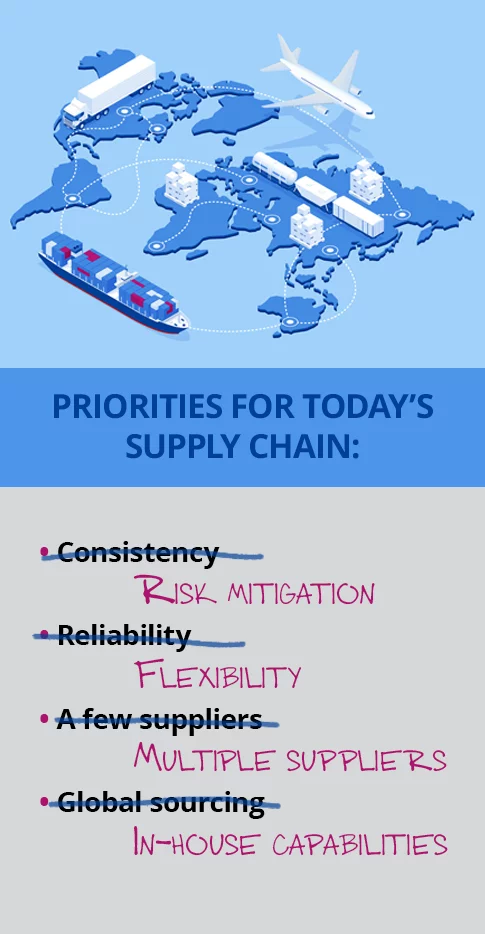
How modular fixtures help manufacturers adapt to a changing workforce
The modern workforce looks a lot different than it used to. The most obvious difference is that employees are now harder to find and much harder to keep.
When considering fixturing options through the lens of changing workforce dynamics, ease of training and workplace comfort rise to the top of the new priority list.
Manufacturers can no longer afford to use the time and talent of veteran staff to train newbies on the use of a complex dedicated fixture. For this reason, modular systems, which don’t require specialized knowledge and can be operated by employees with varying levels of experience, are often a better choice. Their user-friendly designs and intuitive setups offer a distinct advantage by reducing training time and minimizing the impact of workforce changes.
To combat turnover, ensuring the job satisfaction of welders is important — and comfort and safety can play a huge role in how they feel about where they work. While both dedicated and modular fixtures can be designed ergonomically, it’s often hard to predict which operations will cause an issue until a welder repeats those operations over and over.
When modifications are made after the fact, dedicated systems fall short. Modular systems, on the other hand, can be easily integrated with positioning systems that reduce bending, lifting and climbing. Additionally, “open” concept designs, using smaller segments called U-forms, make it easier for workers to reach required welds.
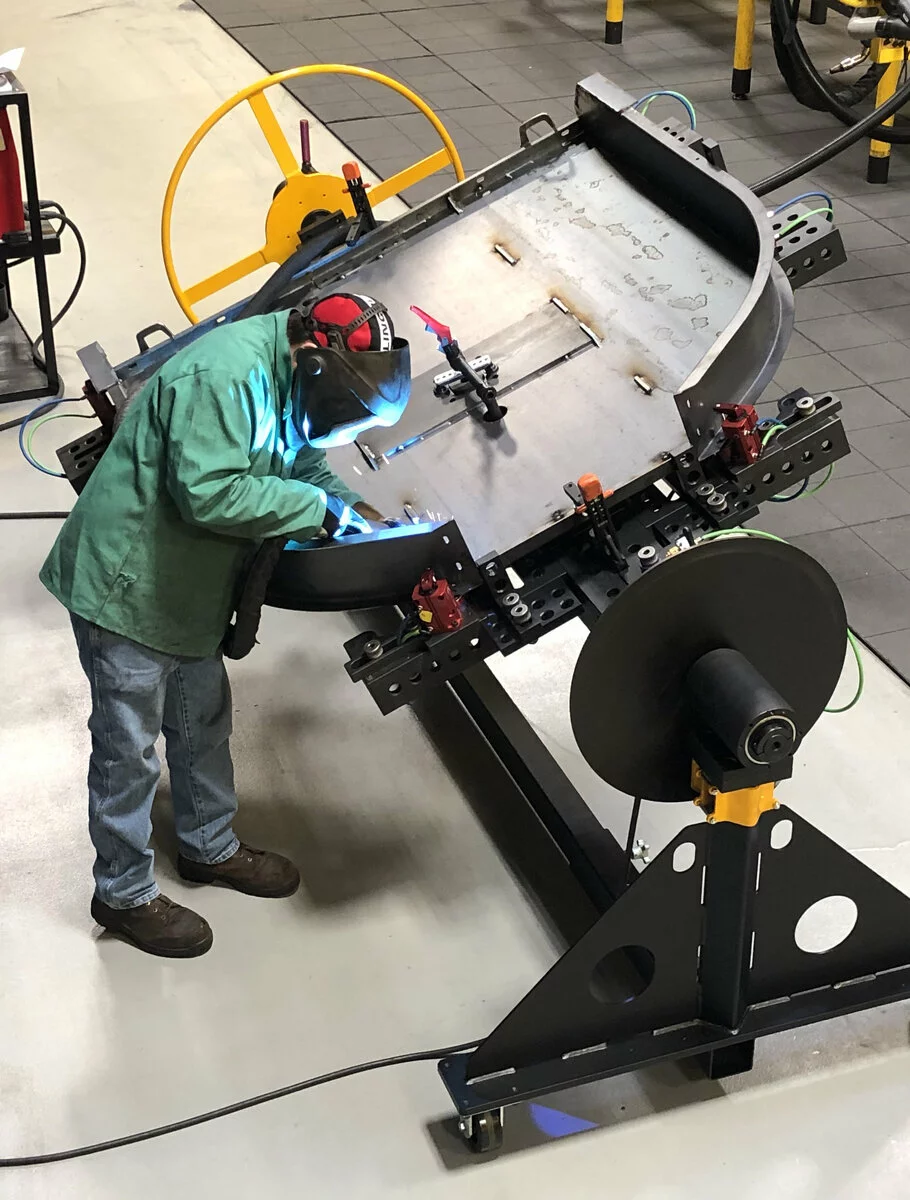
How to decide between modular and dedicated fixturing
We’ve noted some key industry changes and how they might impact your organization. But your goals, challenges and teams are unique. Making the right choice between dedicated and modular workholding systems ultimately requires an analysis of your own situation. Here’s how to approach that analysis:
- Factor in the new variables: With the current manufacturing landscape in mind, consider these key variables (see image 6.1). Which are most important now? Which will be in the future?:
- Work Backwards: Start by considering your end goal. What are you trying to achieve with your manufacturing process? Whether it’s a higher quality product, faster time to market, or both, understanding and quantifying your end goal will help you make more informed decisions.
- Consider the Entire Process: Don’t just focus on the workholding cell. Look at the bigger picture — your process, piece parts, production line, workers, and everything else in your manufacturing area. How will each option impact the overall efficiency and effectiveness of your operation?
- Future-Proof Your Process: With the rapid pace of change in the industry, it’s crucial to choose a system that can grow and evolve with your needs. Plan for scalability that covers changes in market demand, expansion of your organization, etc.
- Rely on Expert Help: Finally, don’t hesitate to seek expert advice. Workholding is a critical component of your manufacturing process, and getting it right can make a significant difference in your bottom line. A trusted expert can help you evaluate your options and make the best decision for your business.
In today’s manufacturing reality, the decision between dedicated and modular workholding systems is no longer as straightforward as it once was. But taking the time to reassess the variables and reconsider the math allows you to align with the demands of the modern manufacturing landscape, and keep your business on course for success.
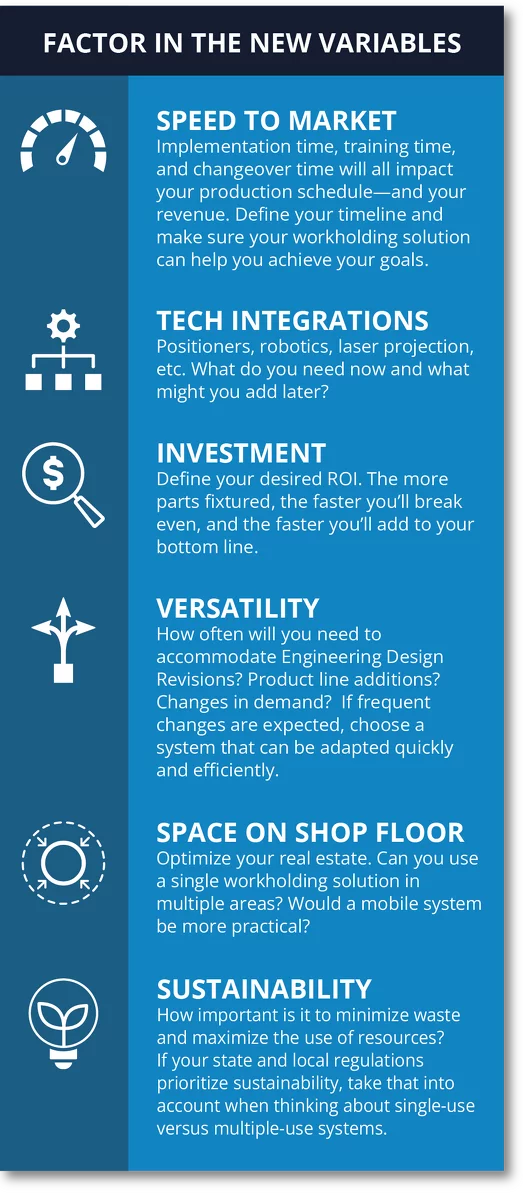