One Size Fits All
Positioning is the key to safer builds for industrial burners in varying sizes
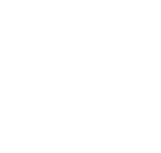
Industry
Manufacturing
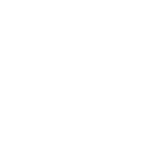
Challenge
Safety
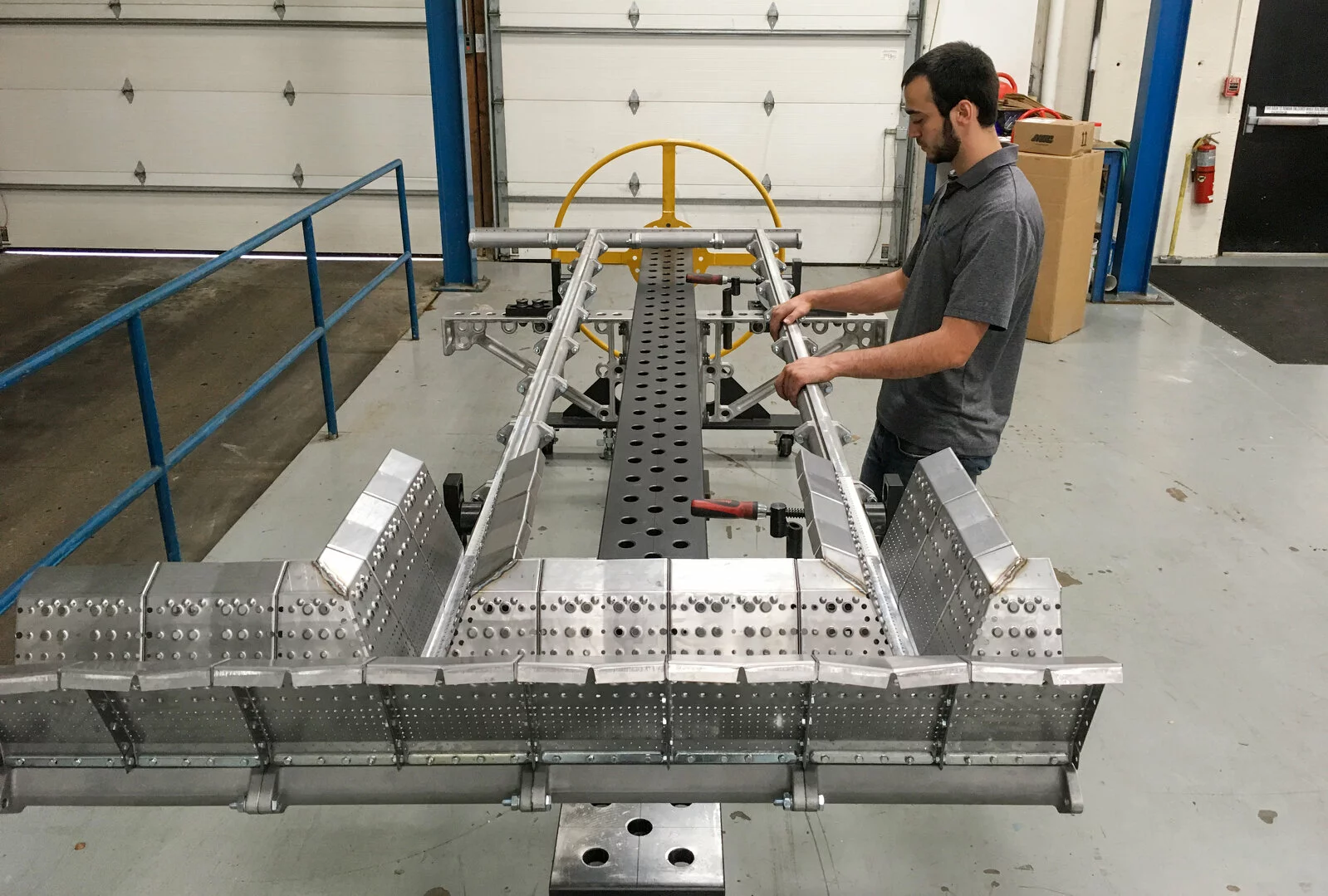
Challenge
Rarely do parts need to be manufactured in only one size. This burner assembly is no exception. It needs to be built in a huge variety of shapes and sizes. The current method involves saw horses,
and too much crouching, bending and laying on the floor to weld. On top of that, sharp edges on the burner deflectors make it tough to roll into various positions safely.
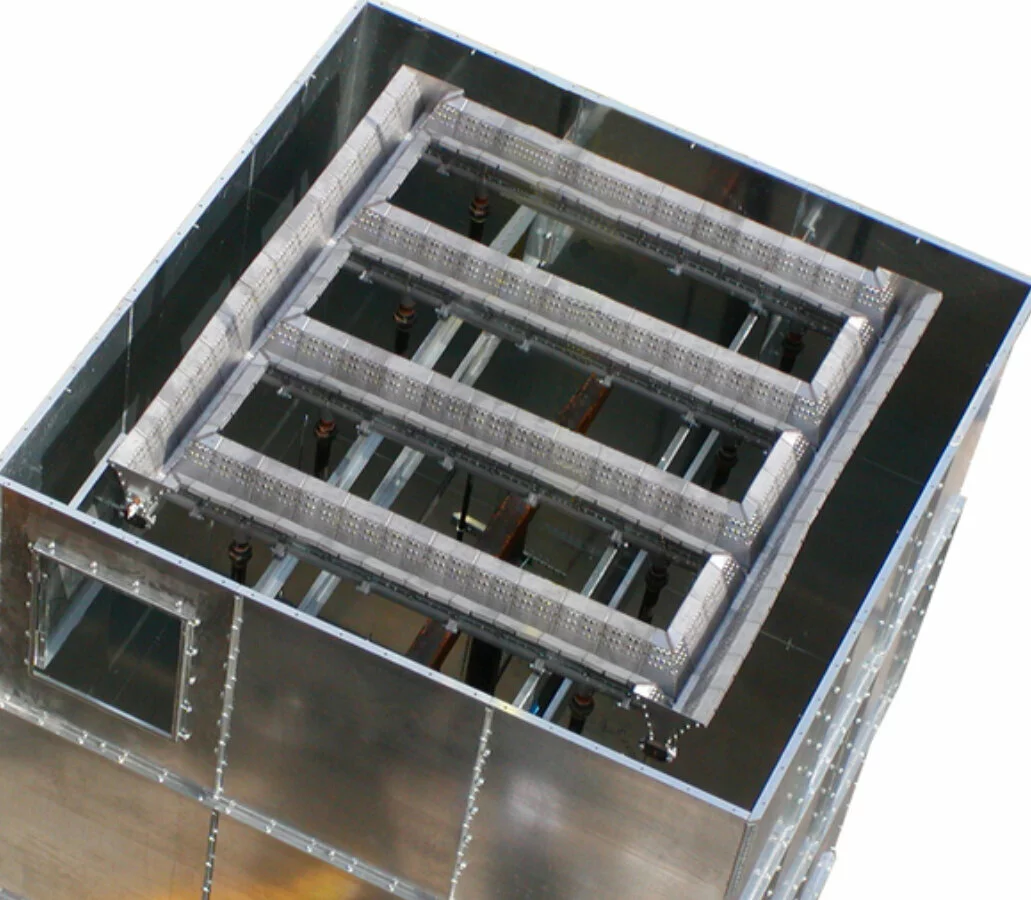
Solution
- Manual Positioner with hydraulic lift assist & air brake
- Aluminum outriggers
- Long beam spine
- Modular tooling kitLarge parts in multiple sizes can be handled on a single spine by using lightweight aluminum angles
as outriggers. Modular clamping components attach effortlessly to the angles to secure parts. The modular kit contains enough tooling to do two small assemblies. Manual Positioner rotates 360° and locks into position.
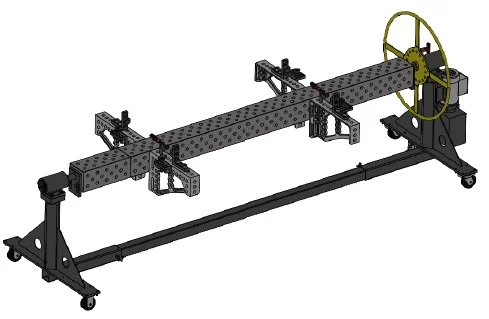
Results
The build starts by loading pre-tacked burner tube assemblies into the fixture and securing with clamps. No CAD models or set-ups are needed. The operator simply moves the outriggers to wherever they’re needed to support the assembled tube. The Manual Positioner allows ergonomic lift and manual rotation for limitless positions and easy assembly of deflectors. No more saw horses. No more crouching, bending or rolling sharp-edged parts by hand.
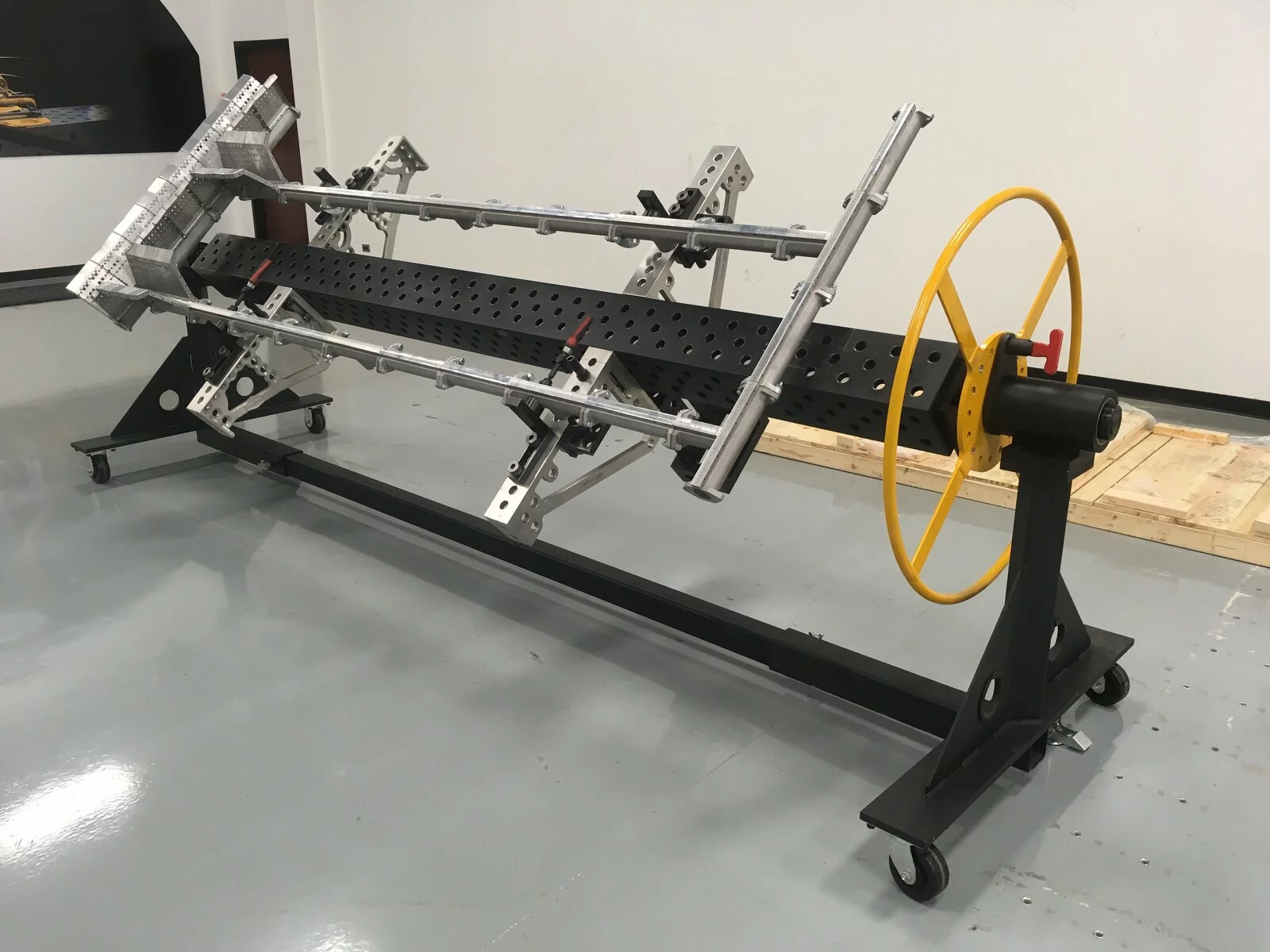

New: Bluprint™
Proposals only show how much it will cost. BluPrint proves how much you can gain.