Detroit Truck Manufacturing
Detroit Truck Manufacturing Gets its Factory Rolling with Bluco
...What most impressed me was that about 3 hours after I sent in the SOLIDWORKS design, I was looking at a fixture model on a video conference call with our Bluco engineer...
Todd Stoughton

Industry
Agriculture

Challenge
Varying Part Sizes
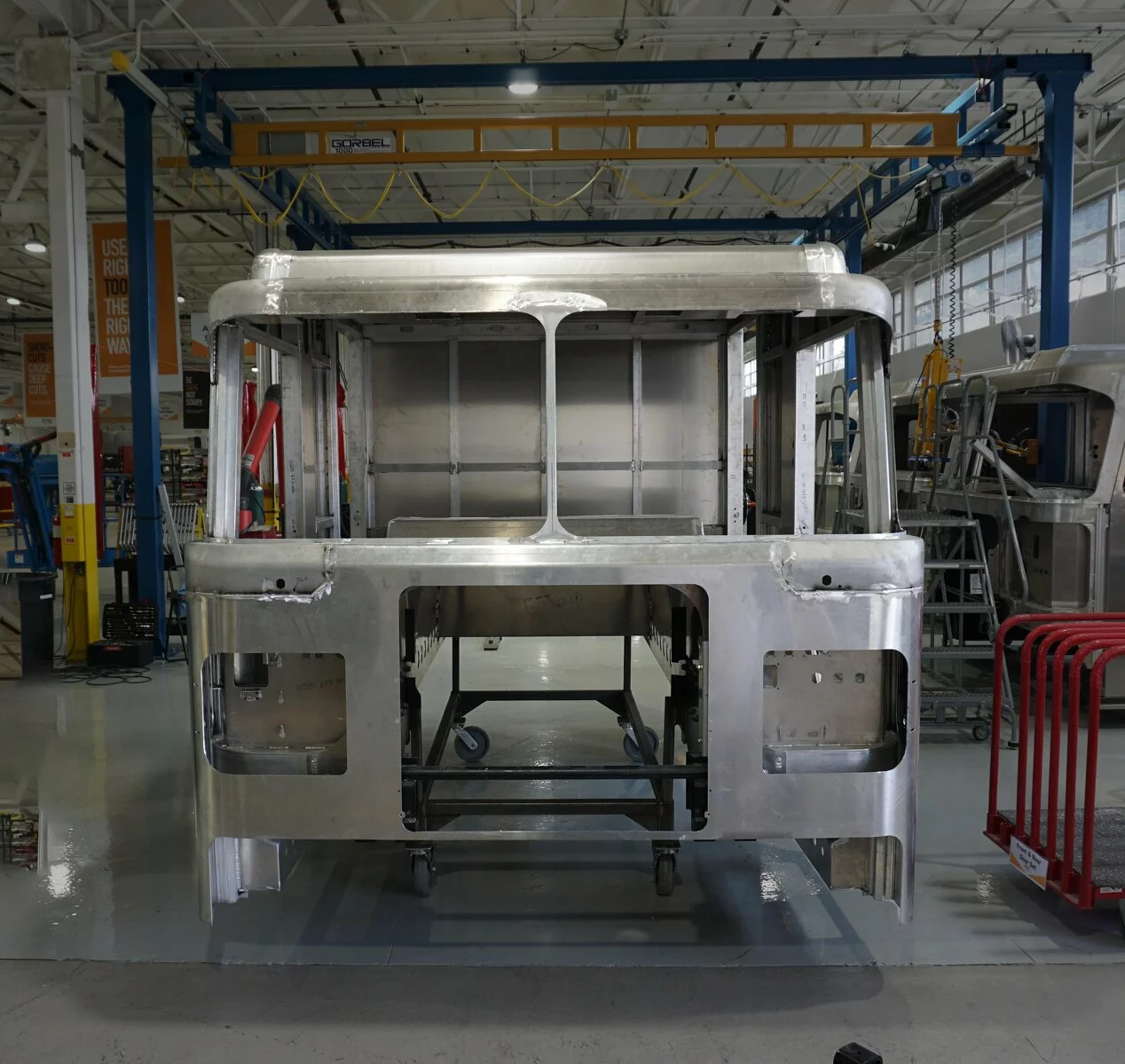
Company Profile
Detroit Truck Manufacturing
Madison Heights, MI
2,300 Employees
Aluminum Truck Cab Fabrication
CHALLENGES
Supply Chain
Wide Variety of Part Sizes
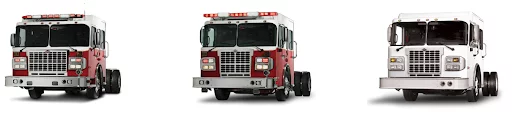
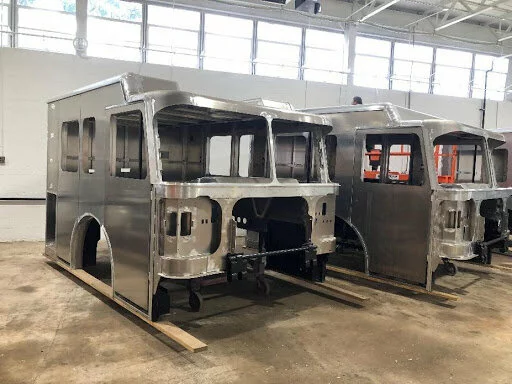
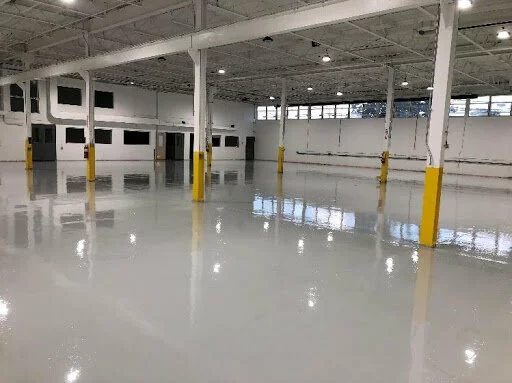
Modular fixturing and teamwork make for a successful solution
To make big changes, companies often have to overcome even bigger obstacles. When faced with such a challenge, Detroit Truck Manufacturing (DTM) called on Bluco and their expertise in modular fixturing for a solution.
In his role as Director of Welding Engineering for Oakland Standard Company, Todd Stoughton got an informed perspective on the entire project from beginning to end.
A manufacturing shift with major potential benefits
The cabs for Spartan Motor fire trucks were being manufactured by another company and then shipped to Spartan’s assembly line. To become more vertically integrated, DTM was launched as a captive-channel supplier of fabricated aluminum cabs for Spartan Motors fire trucks, as well as the cab and chassis product it supplies to over 40 OEM fire truck manufacturers.
But as Stoughton quickly learned, the change would require a highly flexible fixturing solution. “My first challenge was to understand what it was I was building,” said Stoughton. “I came into the project thinking we were just building one kind of cab. It turned out to be a huge number of models and options. I quickly realized that if I was going to use hard tooling to build these things, it was going to be millions and millions of dollars.”
After confirming that suspicion by getting quotes on dedicated fixturing, Stoughton had to start thinking outside the box to come up with a better solution — one that not only fit the budget, but could get them operational quickly while accommodating different cab sizes, variable part shapes, and strict GD&T tolerancing despite tight floor space requirements. Stoughton wondered: “How are we going to make these subassemblies and marry them together with the accuracy that we require?”
The solution is modular
Having worked with Bluco, Spartan’s CEO, Daryl Adams, was already familiar with their high quality, quick turnaround and team of experienced engineers. So Adams asked Stoughton to share the CAD designs with Bluco’s engineers.
After the initial virtual discovery sessions with Bluco, Stoughton put a door in the back of his truck and he and the Spartan team visited Bluco’s Validation Center in Naperville, Illinois for several hands-on demos that provided proof that the fixtures they designed for the CAD models worked on the actual part. “At that point I knew that regardless of what I was trying to build, I had a guy that could put it on a fixture for me,” said Stoughton. The answer was indeed going to be modular fixturing. Now it was time to start designing.
RESULTS
Quick Delivery
Easier Workflow
Budget Met
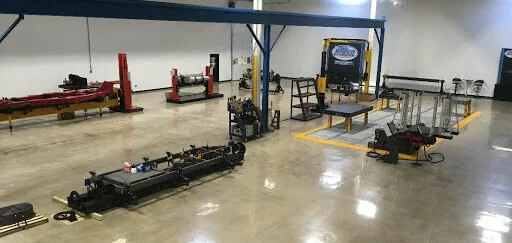
Bluco’s engineers worked side-by-side with DTM to design the custom solutions needed to produce a complete cab. Using ALM lift and rotate positioners and a number of other modular solutions, they came up with a process that worked with the variable part shapes needed, and large final size of the cab. Leaning on Bluco engineers with deep manufacturing knowledge and years of modular fixturing experience, the team had 14 weld cells designed and the full process mapped out in a week.
After the quote was presented and approved, installation kicked off less than three weeks later and DTM was ready to hit the ground running. Multiple cab configurations could be produced and welders were able to safely and quickly access all sides throughout the process.
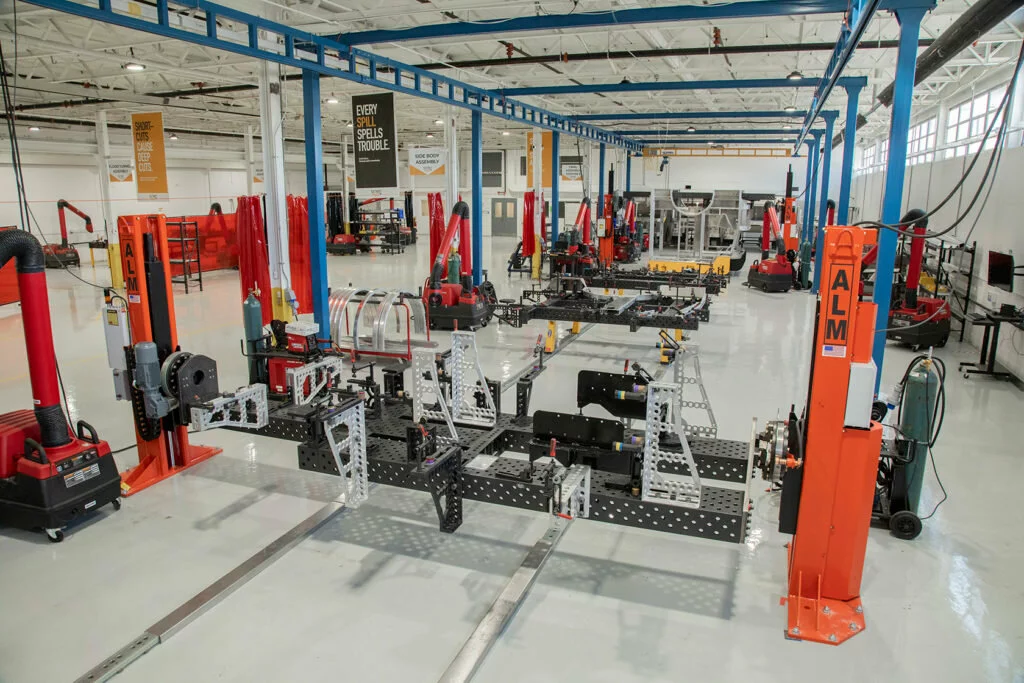
Quick Response
Unique Process
Money Saved
Designs in Hours
Stoughton started out looking for a fixture for one part of the cab — the door. Three hours after he sent in the SOLIDWORKS design, “I was looking at a fixture model on a video conference call with our Bluco engineer,” said Stoughton.
It was literally faster than the other guys could even call me back. I looked at the model and thought, wow – that will work.
Solutions Proved Out in Bluco's Validation Center
After the initial virtual discovery sessions with Bluco, Stoughton put a door in the back of his truck and he and the Spartan team visited Bluco’s Validation Center in Naperville, Illinois for several hands-on demos that provided proof that the fixtures they designed for the CAD models worked on the actual part.
At that point I knew that regardless of what I was trying to build, I had a guy that could put it on a fixture for me.
An Impossible Budget Made Possible
Bluco’s engineers worked with DTM to design a custom solution to produce a complete cab. The final design included modular floor rails, custom welding tables and ALM positioners The team had 14 weld cells designed and the full process mapped out in a week.
It saved a tremendous amount of money. I really don’t even know if this project would have been financially possible without Bluco.

New: Bluprint™
Proposals only show how much it will cost. BluPrint proves how much you can gain.