2X Faster Production with a Future-Proof Modular Fixture System
How a Modular Fixture System Helped Progress Beat Tradition

Industry
Agriculture
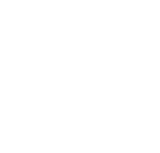
Challenge
Final Part Quality
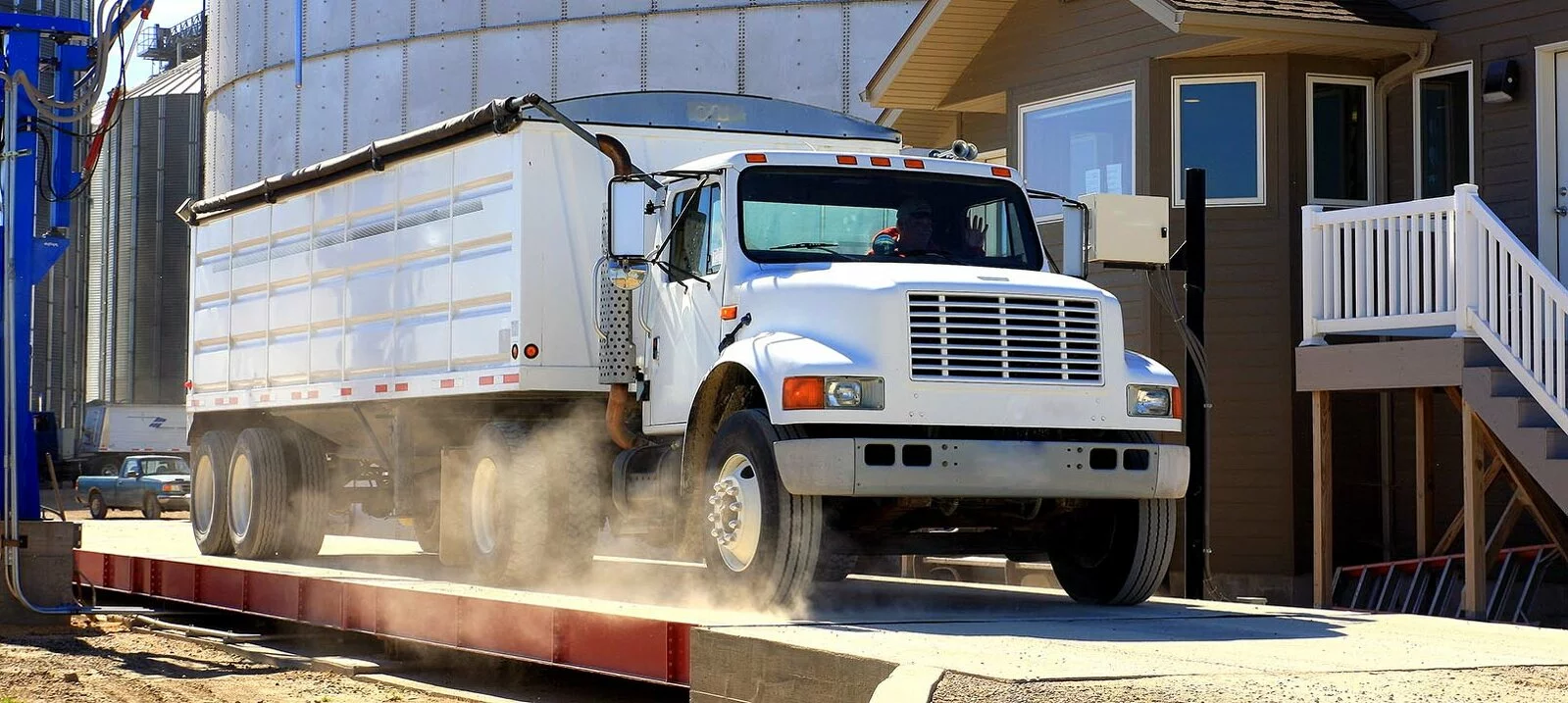
Challenges
Tradition can be comforting, but when it comes to manufacturing, doing it like it’s always been done is limiting. Following the old playbook left this customer struggling with the persistent issue of warped truck scale sub-assemblies produced on a century old fixture. They wanted a faster, more efficient, and more precise method of tacking endplates. They also hoped to future-proof their setup so that a robotic welding fixture could be introduced later. And most importantly, they wanted a modular fixturing system that their welders were comfortable with.
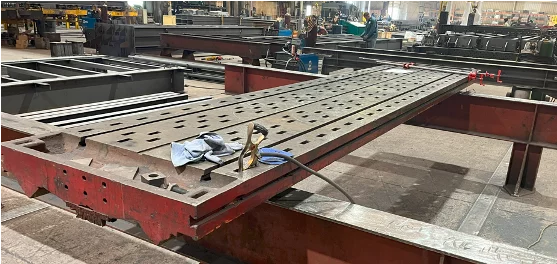
Bridging the Engineering Gap
Bluco’s team focused on the most obvious gap in the customer’s otherwise highly engineered process: their 100 year old workholding methods. The outdated fixture was replaced with something far more 21st-century: a modular fixture system between an ALM lift & rotate positioner.
Color-coded spacers on adjustable posts provided the flexibility needed to prevent warping issues while working on plates of any size. This modular fixture also streamlined the current tacking process and could seamlessly integrate into a future robotic welding cell.
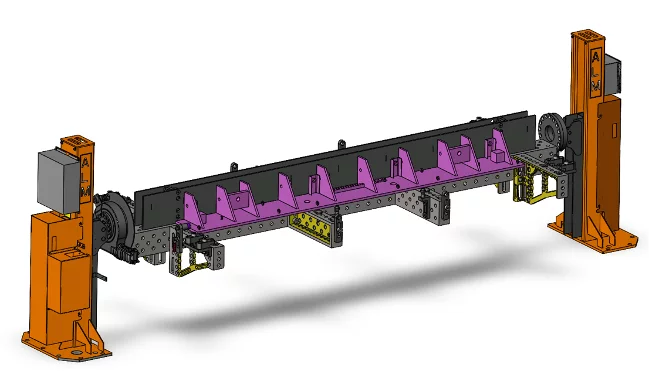
Projected X-Factor Improvement
The welder was initially skeptical of the new setup. However, once he experienced the comfort and ease that came with the ability to lift and rotate the modular fixture, he became a convert. The end result? Welded parts that come together twice as fast. Because the new modular fixturing system keeps them straight and flat, there’s a seamless transition to the next production cell — no time wasted on chain clamps or torch work to make the parts fit. The welder loves his new “toy,” and the company is well-positioned for future automation and efficiency.
Ready to discover YOUR X-Factor?
Connect With Our Team to learn how BluPrint can help you tap into the hidden potential in your production process.
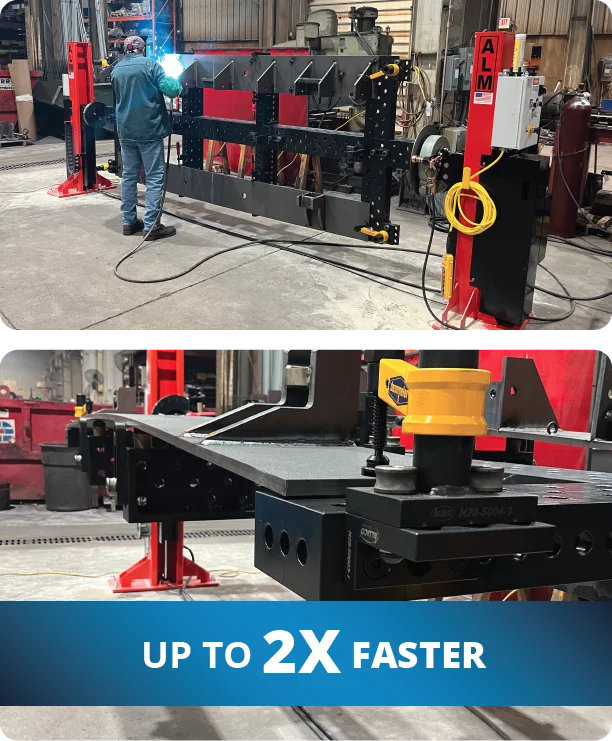

Discover Bluprint™
Proposals only show how much it will cost. BluPrint proves how much you can gain.