Think Outside the Box...and Upside Down
New process, new workholding, new levels of success
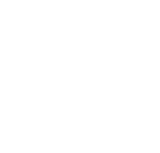
Industry
Transportation (General)
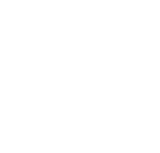
Challenge
Limited Space
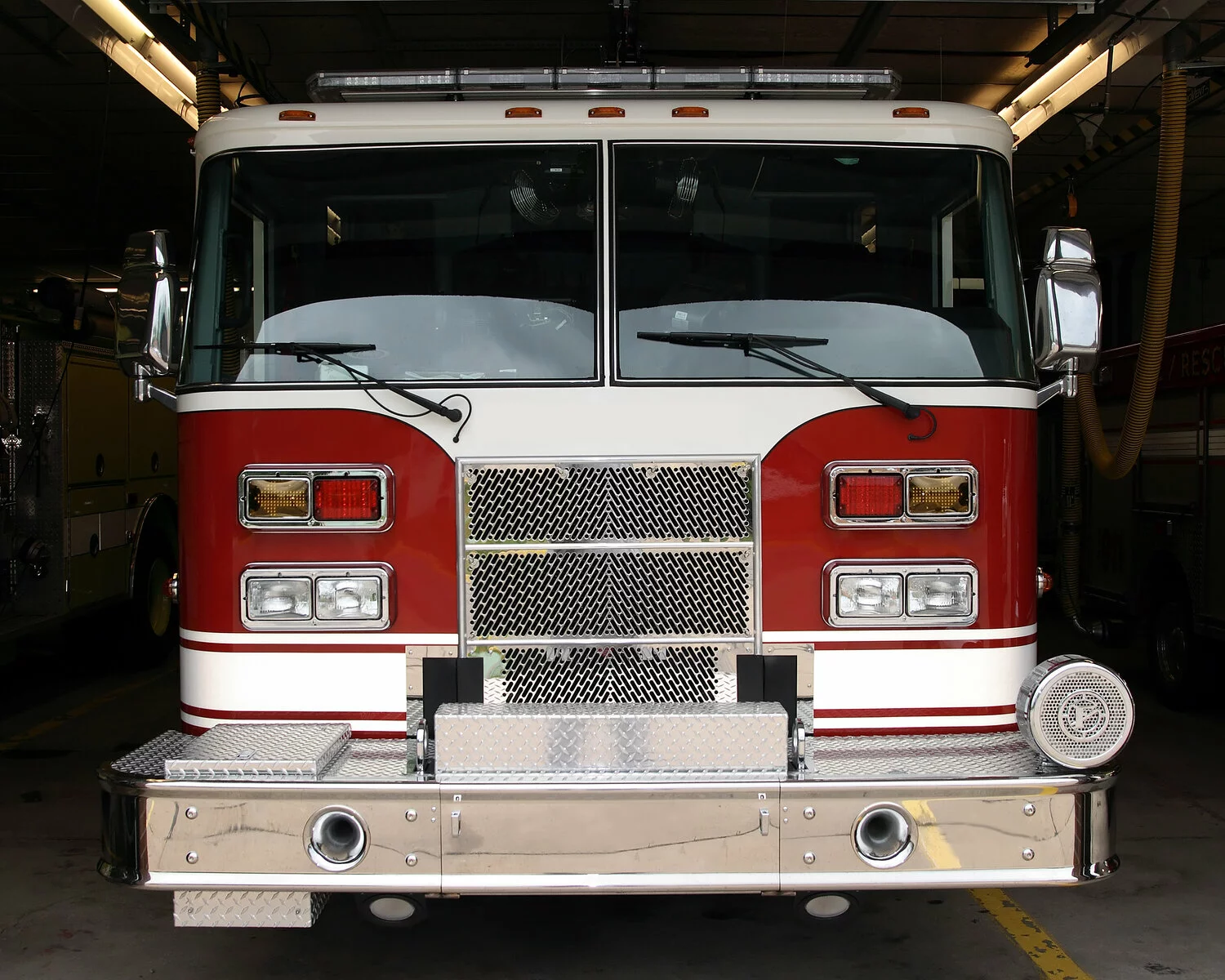
Challenge
Fixturing for the roof of a fire engine cab that’s over 8’ tall is challenging on its own. Add to that a small fabrication area and it gets even harder. Most of the gluing and stitch welding was on the underside of the roof, upside down. The small shop size meant movement of the cab would have to be limited, and since there was no room for ladders or lift platforms, workers had to stay on the ground.
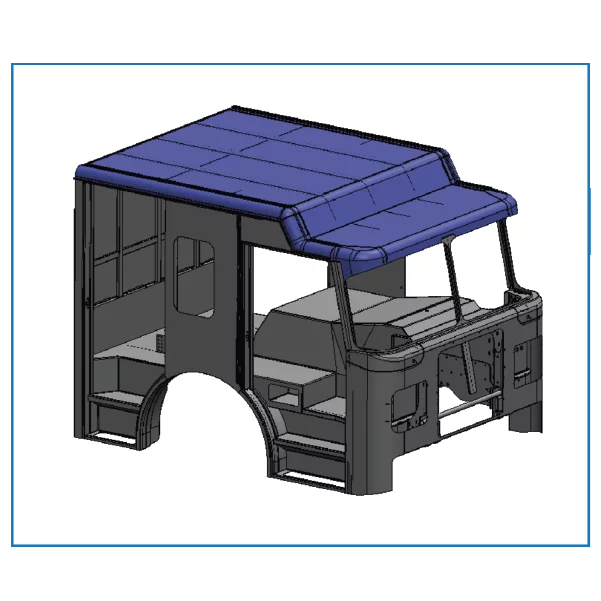
Solution
- Rail system
- Lift & rotate positioners with integrated modular tooling
The cab walls were going to be built on a u-form fixture already, so step one was to adapt those fixtures, the floor, and now the roof all to a rail system. This was accomplished by integrating modular tooling between ALM positioners. Step two was the decision to fixture the cab upside down, to take advantage of “free” pressure provided by the weight of the cab and tooling.
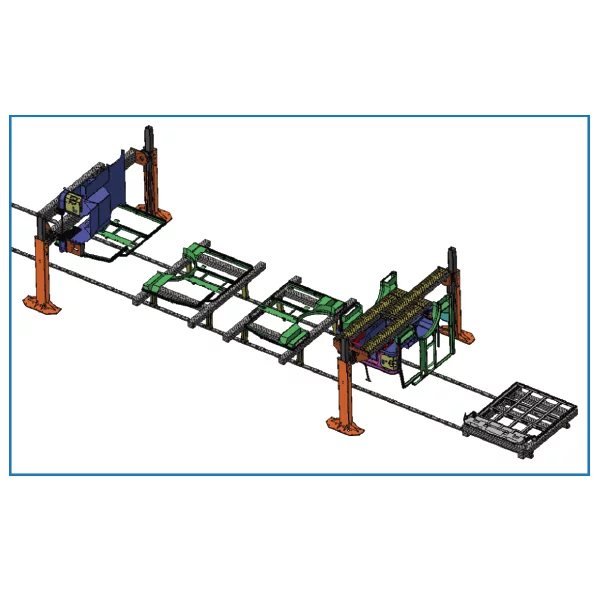
Result
Ultimately, the roof challenge helped create a total solution that married the entire process , including cab sidewalls and floors, into one elegant solution. The system eliminated the need for crane handling, kept welders’ boots on the ground, provided a good line of sight for alignment and significantly sped up production. In addition, flipping the cab made for a shorter fixture and additional space savings.
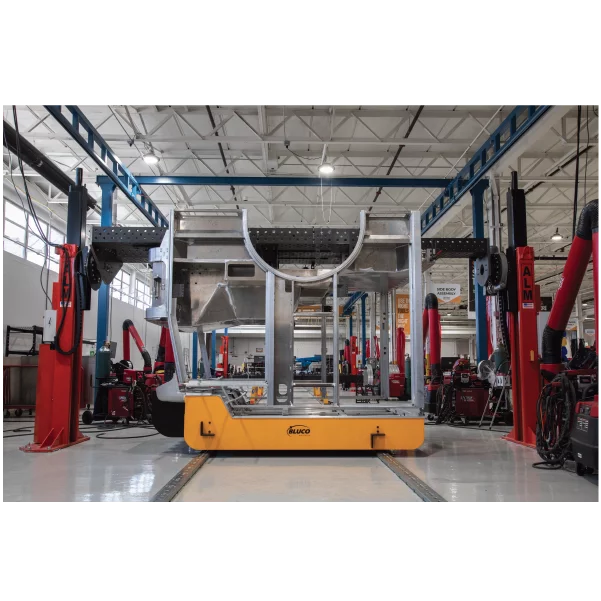

New: Bluprint™
Proposals only show how much it will cost. BluPrint proves how much you can gain.