New Process, Better Results
To build train cabs faster, focus on sub-assembly fixturing
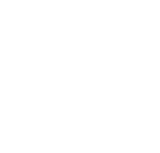
Industry
Transportation (Railroad)
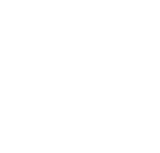
Challenge
Speed to Market
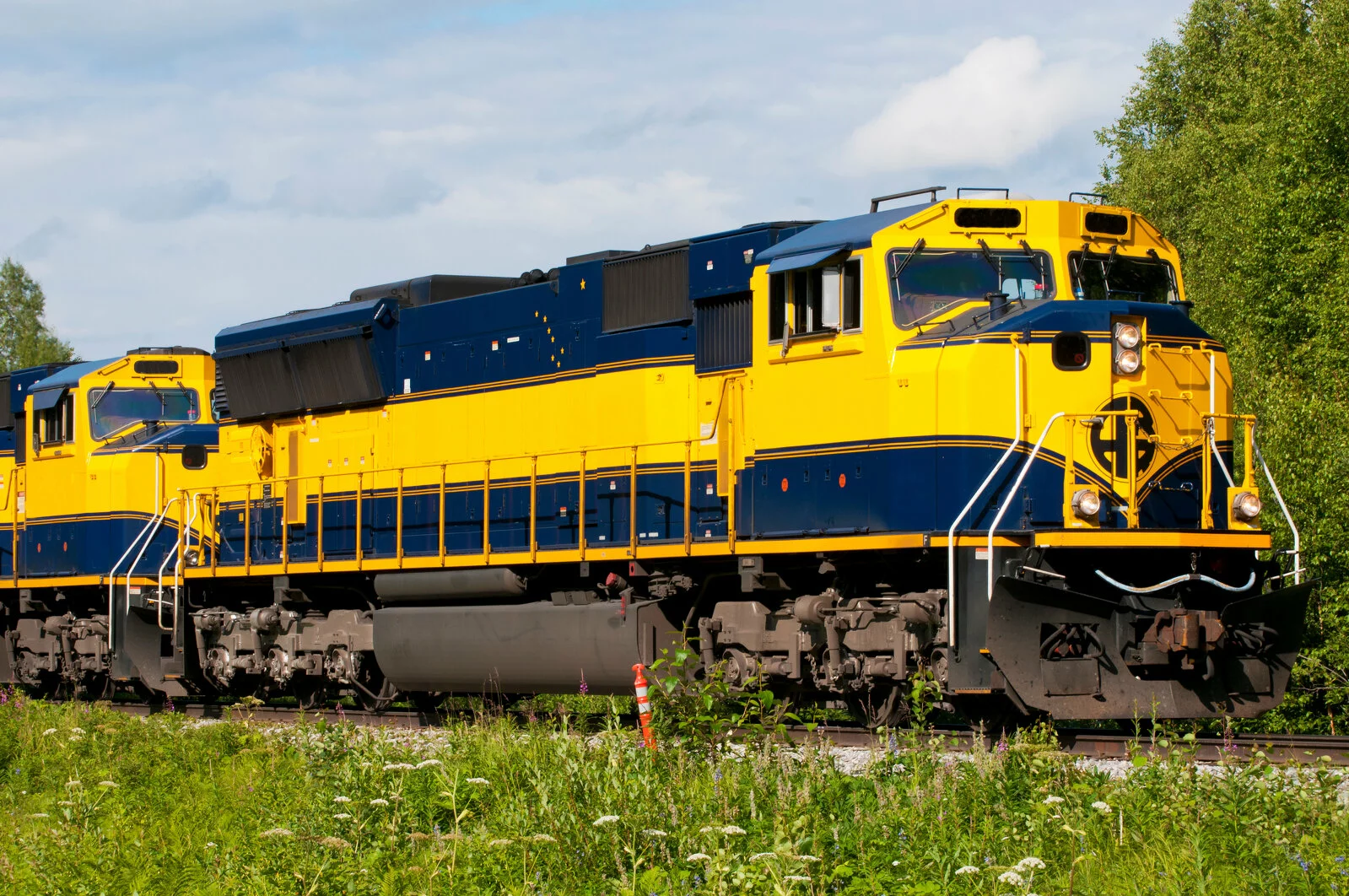
Challenge
Not every challenge is about a fixture. Sometimes, it’s about redefining the challenge itself. In this case, the initial ask was to design a fixture to marry the subassemblies for a train cab.
Time was tight, and because there were only three different prototypes to build, dedicated fixtures weren’t an option. To win the production contract this company had to get everything right.
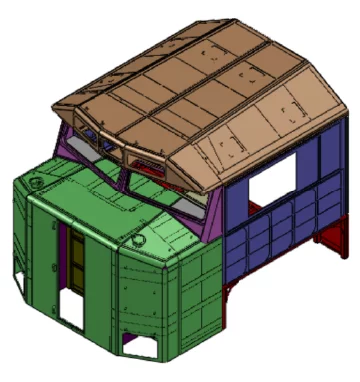
Solution
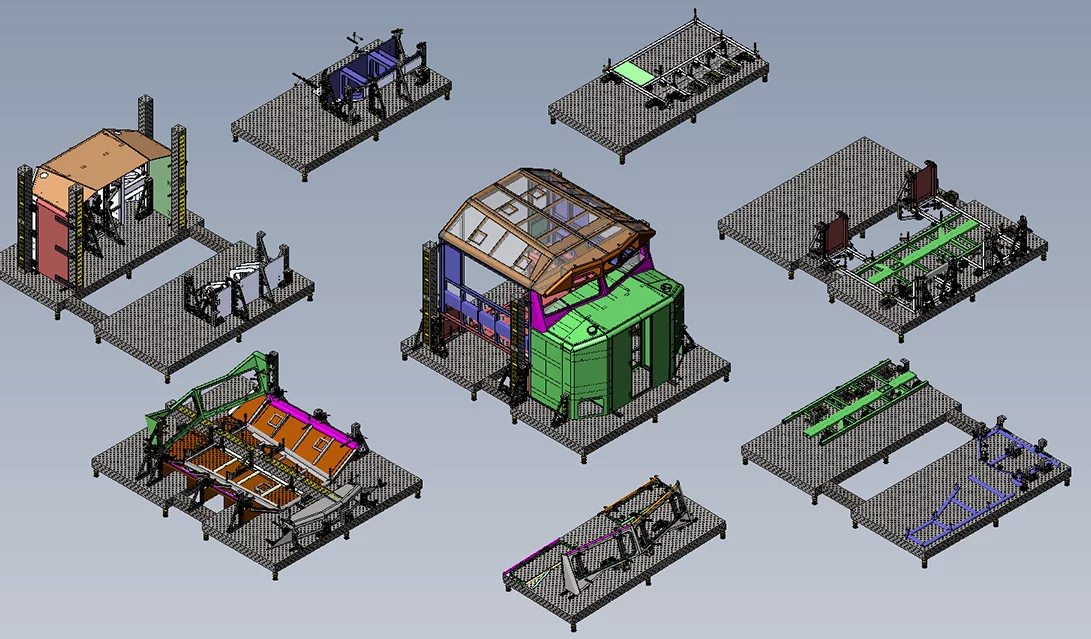
- Two large Custom Welding Tables
- Kit of standard modular components
- A new plan: fixture the subs AND the final part
A tailored package of modular tooling and two large tables allows sub-assemblies to be built in groups of three. Once the 11 subs are built, the same system is used to assemble the cab, answering the original request. CAD designs with setup instructions for each build are accessed from a tablet on the shop floor.
Results
Fixturing experts delivered repeatable designs for every sub. Prototypes are built faster than originally quoted for production, with the final marriage of subs only taking 4 hours rather than 4 days. The time savings translated to a lower selling cost to the customer. Finished interior panels fit like a glove.
Customer Quote:
“We originally thought we wanted to use the modular tooling for just the final marriage cell. You have proven that it was better to use it for all the subassemblies. When the subs are all made correctly the marriage is a piece of cake! Everything fit like it was supposed to. Well done Bluco!”
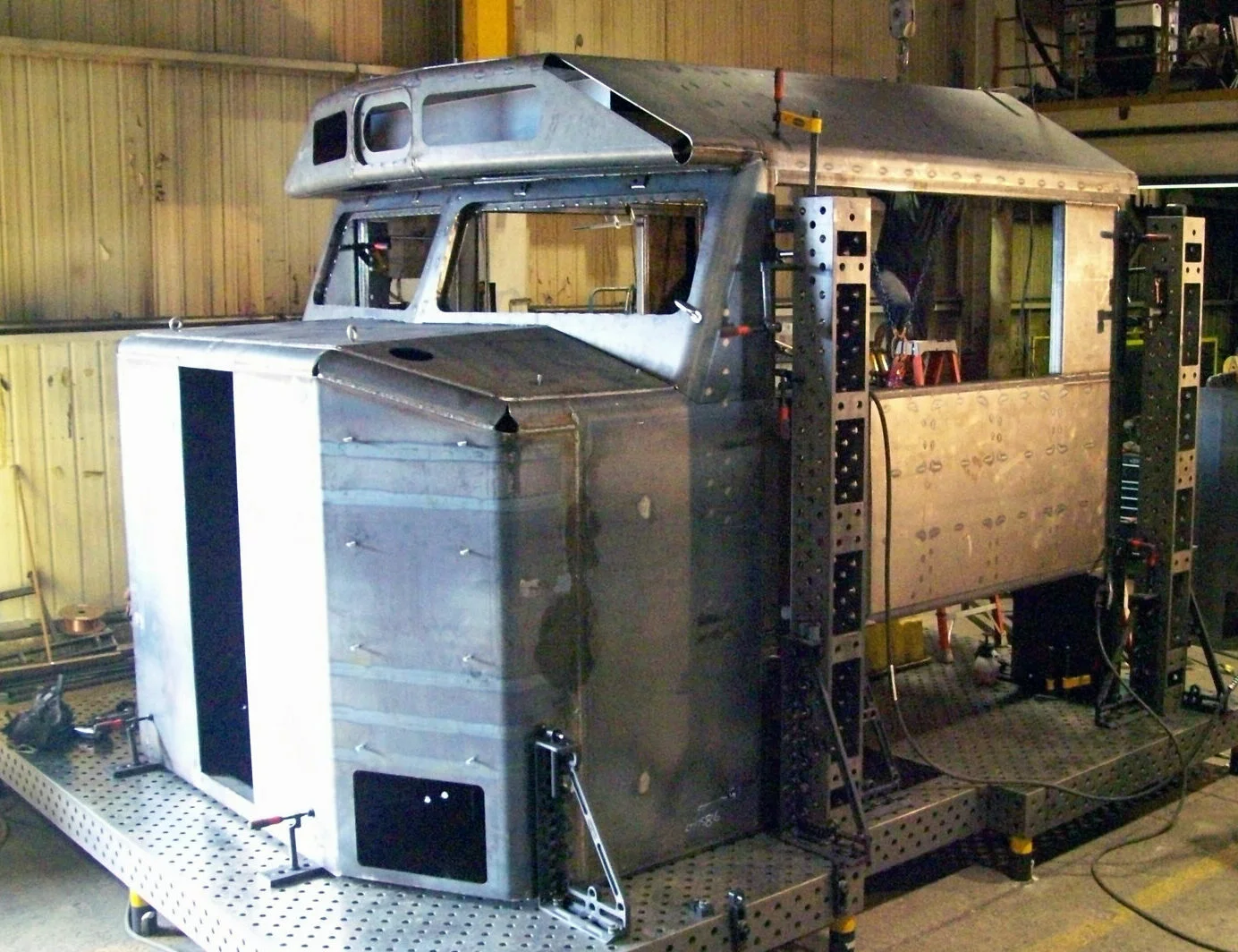

New: Bluprint™
Proposals only show how much it will cost. BluPrint proves how much you can gain.