Skip the Heavy Lifting
Modular positioning improves safety, efficiency and quality
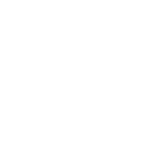
Industry
Mining
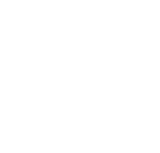
Challenge
Unusual Parts
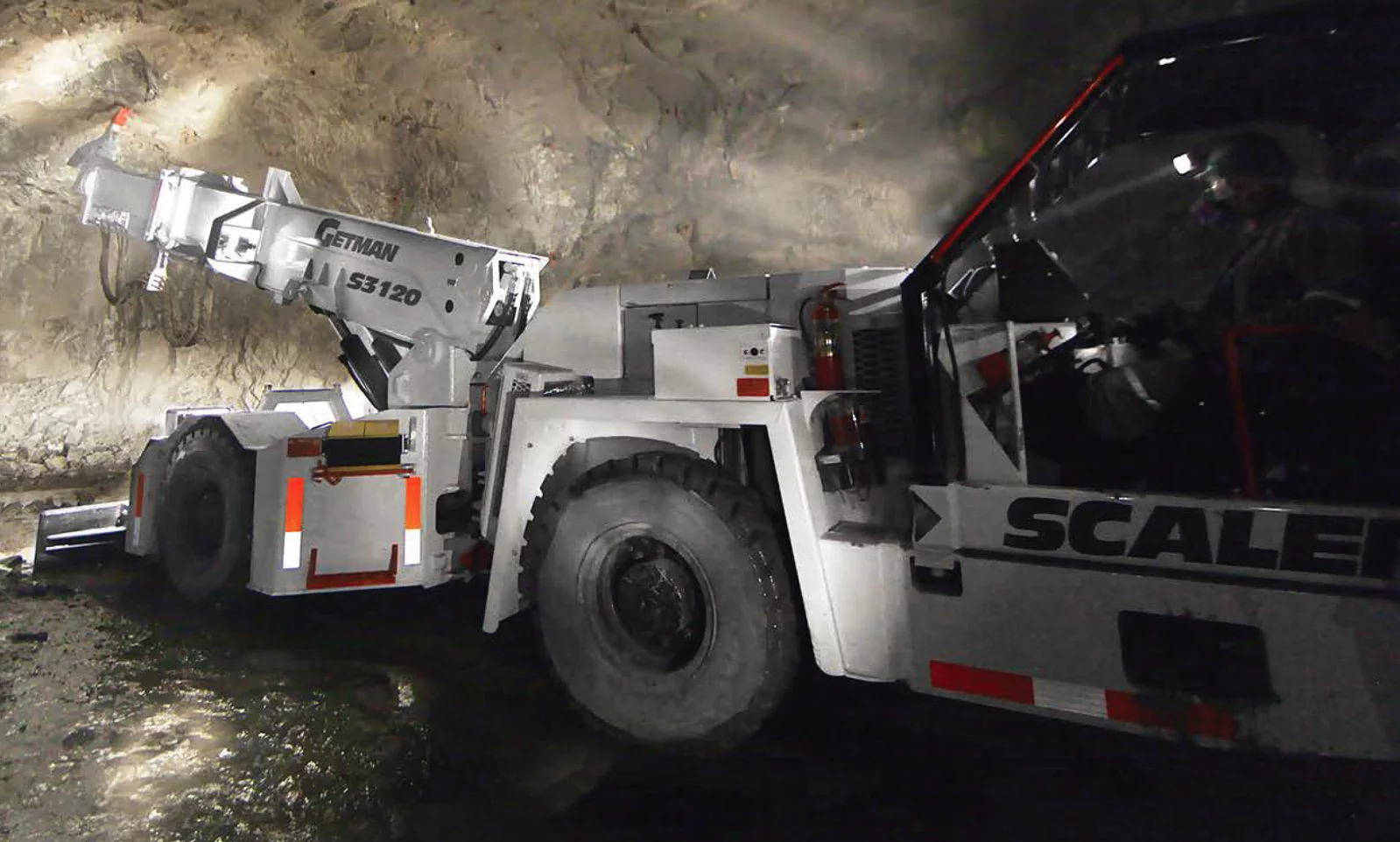
Challenges
Some parts just seem to be the perfect storm of all the attributes that make them difficult to weld: an irregular shape, enormous weight, a lack of any good hook points, and rounded areas that make it hard to hold without rolling. Add to that some hidden welds that have to be made before the next piece can be added. How do you hold a piece like in the correct position to weld?
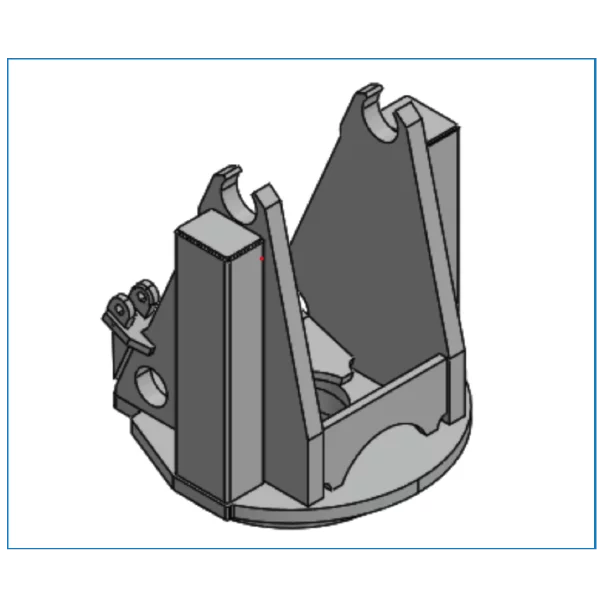
Solution
- Powered Manipulator
- Teach Controller
The answer is to start with positioning. No matter what, a heavy part is always going to present challenges unless you can move it into whatever position is necessary. For that, a powered manipulator provides the ability to lift, tilt, and rotate your part in its fixturing. Irregular shape and lack of hook points are no longer issues, and you get weld access from every angle. Adding a teach controller allows you to save positions for efficient, repeatable moves.
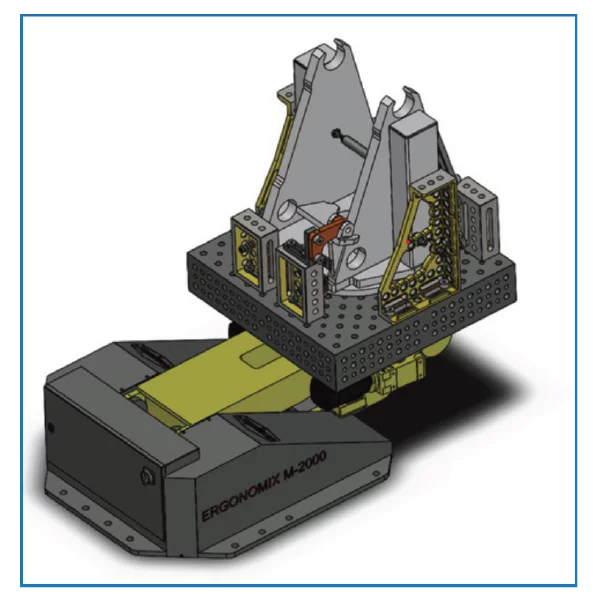
Result
This solution increases safety and improves welder comfort by eliminating heavy lifting and positioning the part more ergonomically. It also allows the part to be tacked together in the positioner, freeing up a tack cell and fitter for other work. Modular fixturing enables a progressive build of the part while it’s still in the fixture, which results in higher quality welds and faster throughput.
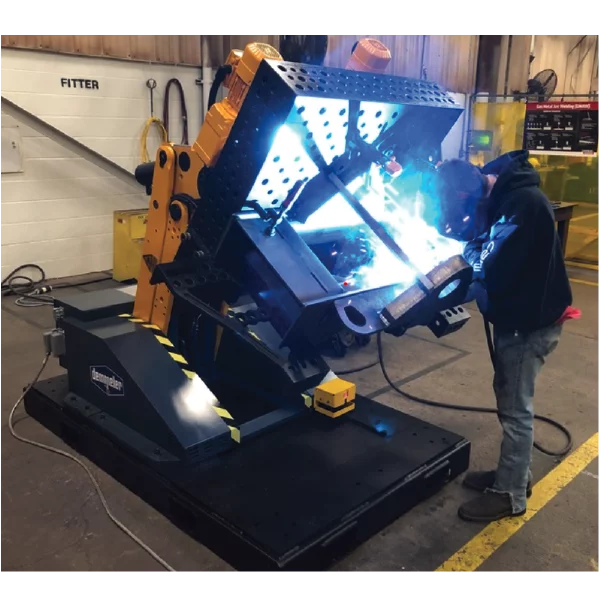

New: Bluprint™
Proposals only show how much it will cost. BluPrint proves how much you can gain.