25% Less Cost, Priceless Safety Improvement
Solution solves for varying part size, hard-to-reach welds and worker safety

Industry
Agriculture
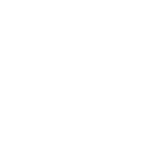
Challenge
Safety
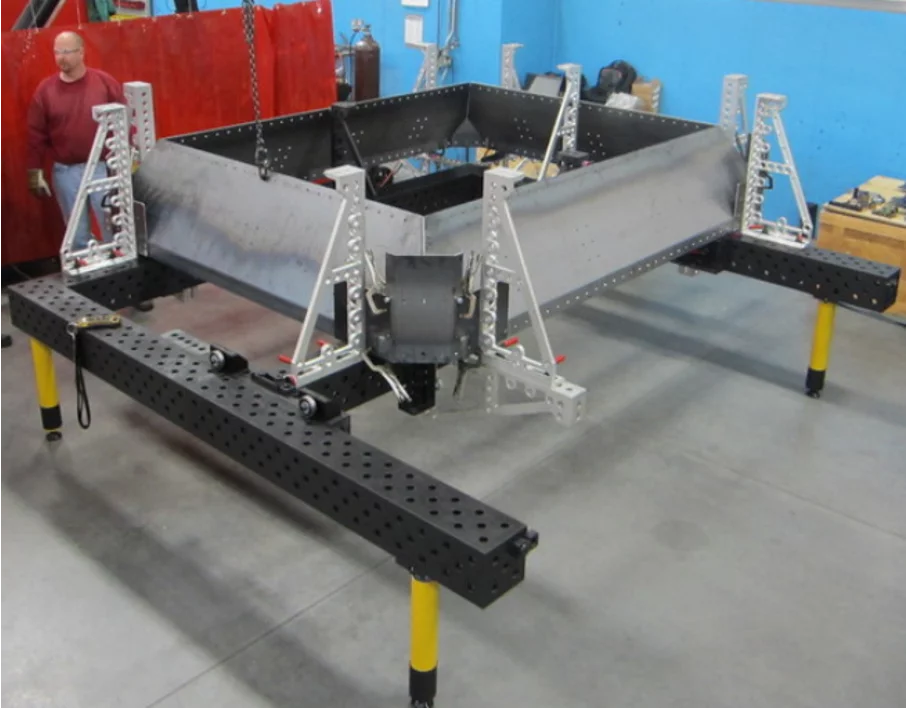
Challenge
Parts that vary in size and need to be made one at a time are always a challenge, and this line was no exception. Ranging from 3’ to 12’ square, welders also needed to access each corner, and the inside and outside of the weldment. A larger table wasn’t the answer, since that would require welders to climb on top or kneel on the ground. And of course, accuracy mattered — holes in the panel needed to align for assembly later.
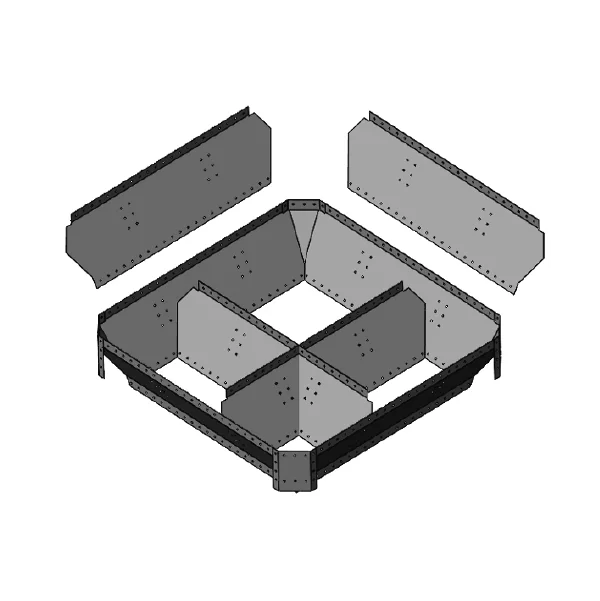
Solution
- U-form system
- Roller bearing assembly
The key to this solution is to open things up. Working with an open u-form structure instead of a table allows welders to access the part from all sides. U-forms slide on roller bearing assembly to accommodate differing part sizes., while anchored legs secure the four corners. Custom hybrid adapter plates align holes accurately every time.
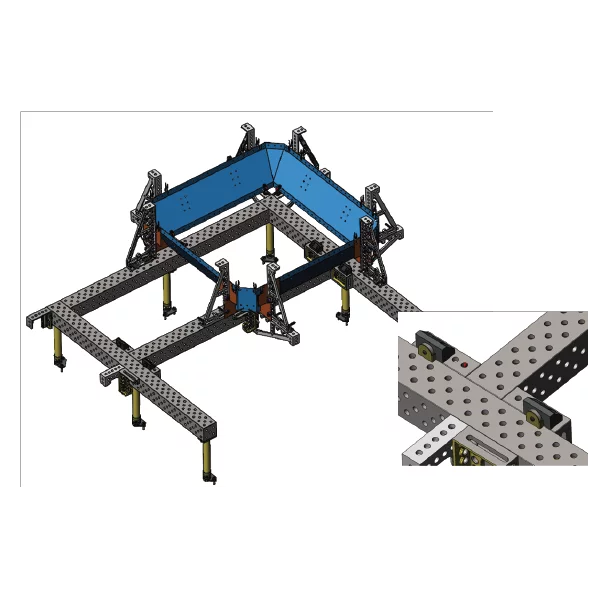
Results
The open concept allows welders easier access to all sides of the part. The u-form system also puts parts at the perfect height for increased comfort, and keeps boots on the ground, eliminating the need to climb on the table. The simple yet elegant design and innovate roller bearing system make for quicker changeover. The use of u-forms also means a fixture cost reduction of 25% over a 12’ square table fixture.
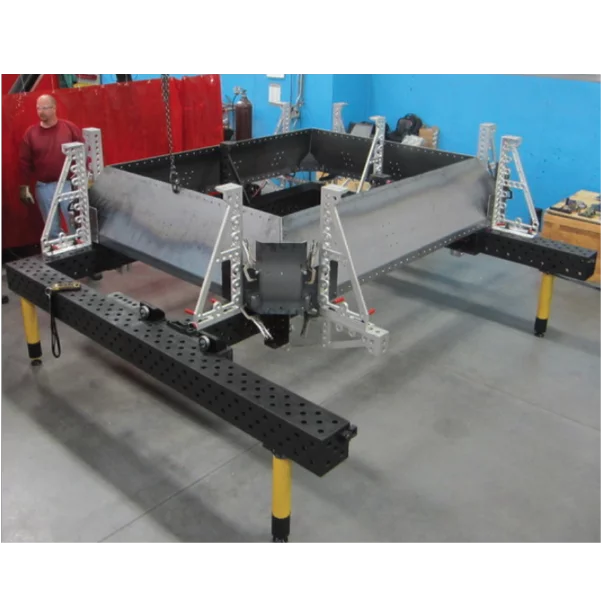

New: Bluprint™
Proposals only show how much it will cost. BluPrint proves how much you can gain.