Z Modular
DOUBLE OR NOTHING
When doubling production is the only way forward, the solution is modular
We needed a solution that would allow us to hold everything together while we welded it into place, keeping it within our tolerances.
MATT MILLER, PLANT MANAGER
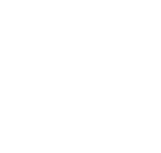
Industry
Construction
Challenge
Throughput
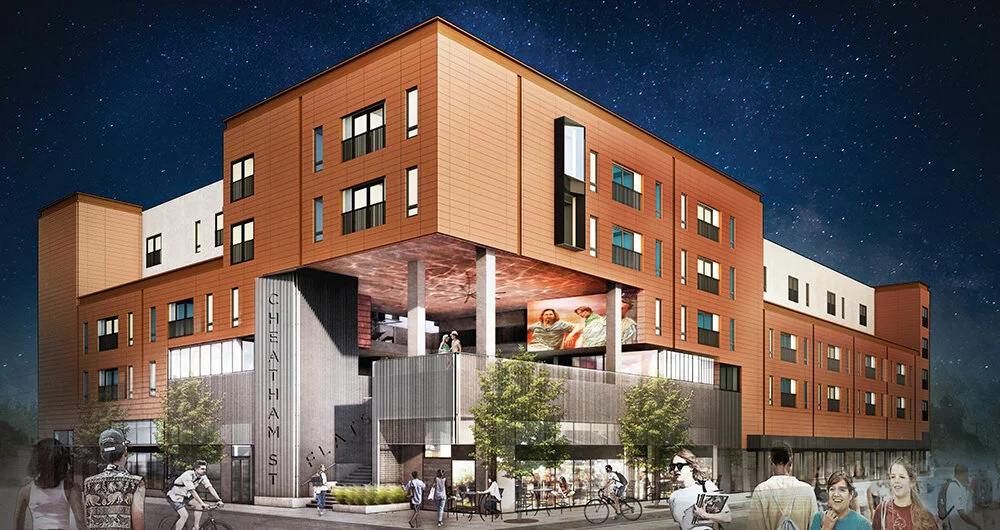
Company Profile
Z Modular
Chandler, AZ
180 employees
Modular Construction
Challenges
Infinite part sizes
Need quick delivery
Need to increase throughput
Blend two fixtures into one cell
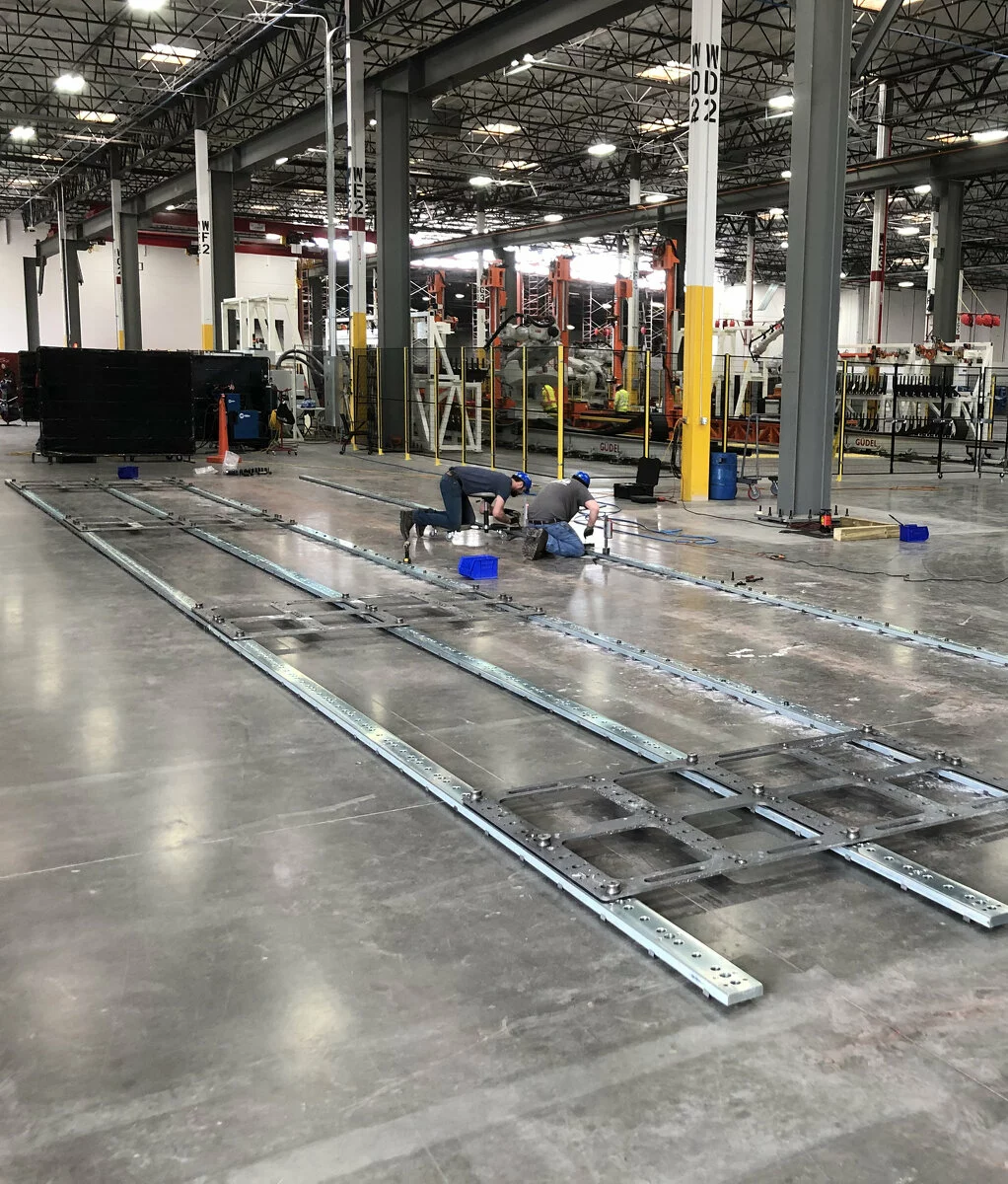
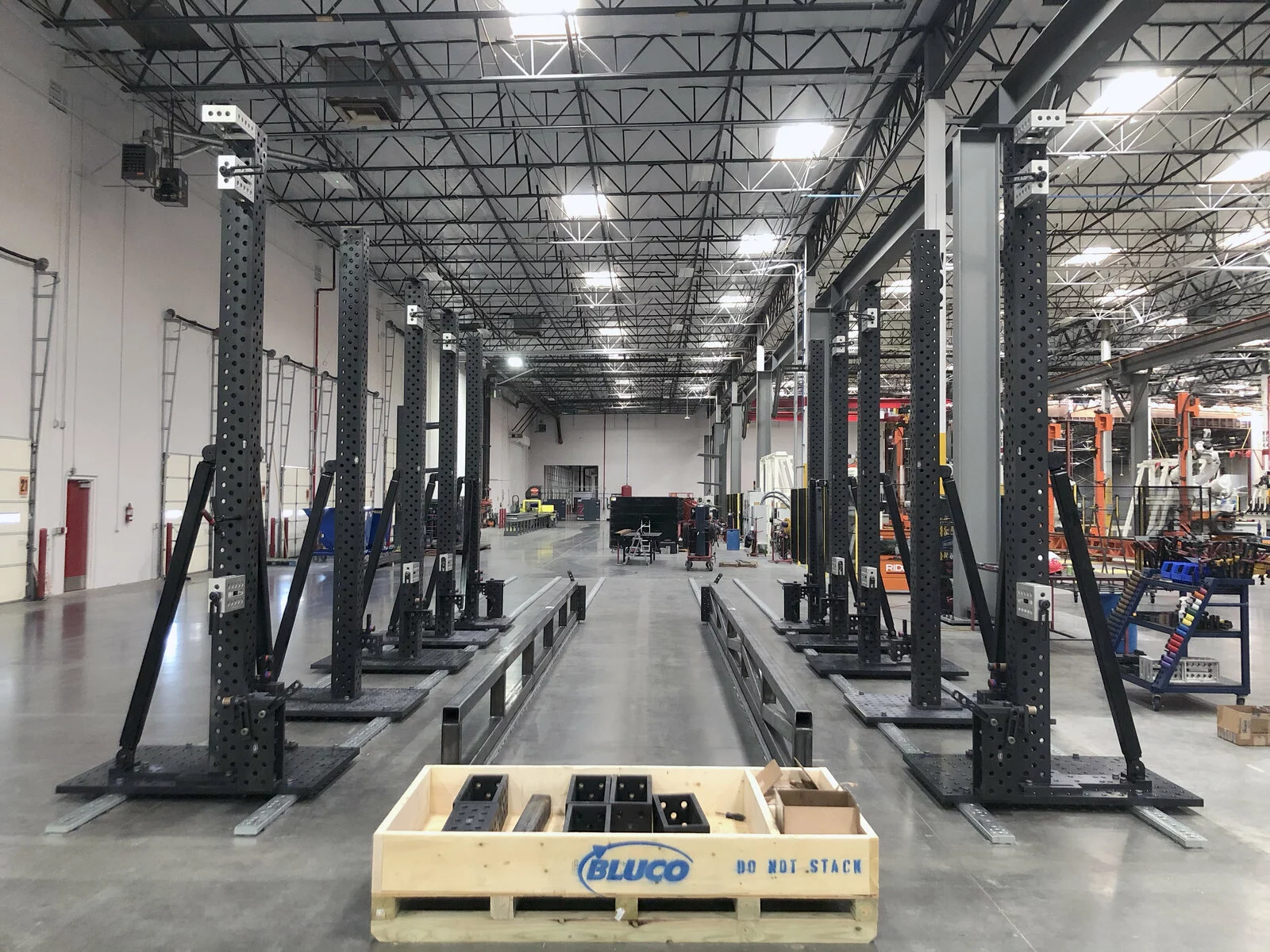
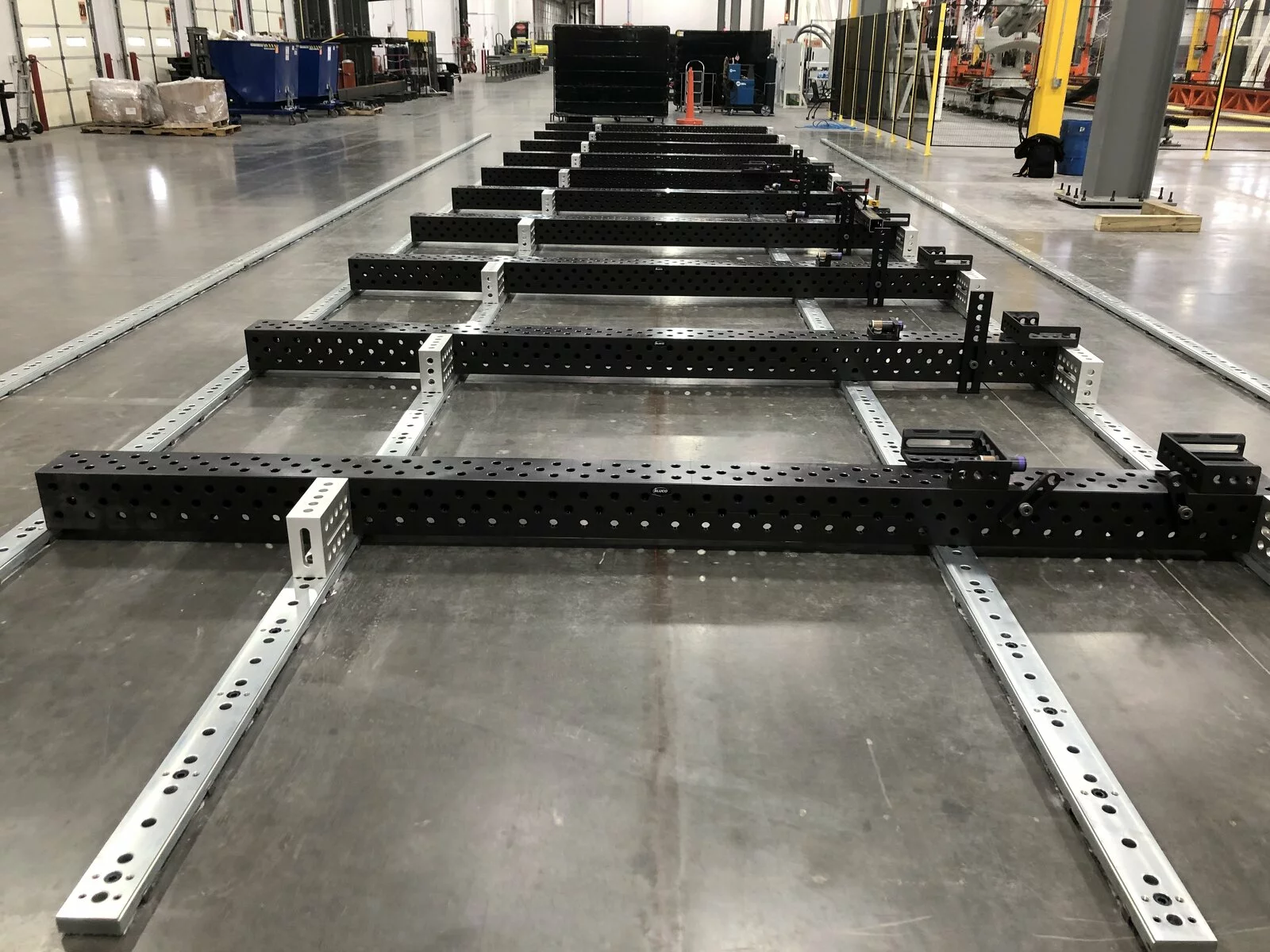
They were committed to achieving the impossible …
When Zekelman Industries announced the launch of their Z Modular facility in Arizona in 2019, they had a goal that few would be able to reach successfully. They would deliver steel-framed volumetric modular building units up to 50% faster, without cost overruns, built to 1/16” tolerance. In a nutshell, their goal was to deliver the golden trifecta to the construction industry: fast, affordable and very, very good. They had most of the ingredients they needed to get it done.
The Arizona facility would be Z Mod’s third, so they’d been down this road before. They would be producing 90% of the raw materials needed for construction, including the steel (Zekelman’s specialty), so timelines were mostly under their control. And they had a knowledgeable team in place. The plan was to eventually rely on automation to deliver the speed they needed to take them over the top.
But Matt Miller, Z Mod’s Chandler Plant Manager, wanted to establish that speed even before the automation came online. “Not only that,” says Miller, “but there were also the usual factors that are just a part of modular construction, including the need to fixture for an infinite number of size variations.” For all that, in Miller’s mind there was only one solution.
Z Modular turns to Bluco modular
When Zekelman Industries announced the launch of their Z Modular facility in Arizona in 2019, they had a goal that few would be able to reach successfully. Being a modular company themselves, a modular fixturing solution made perfect sense to Z Mod. They knew that for high mix, low volume production, there was simply no better choice.
“I knew we needed a modular system because we build so many different assemblies with different dimensions,” says Miller. “We needed something that was flexible, so we could move the tooling around quickly and easily.” He also needed someone with experience to nail what he knew would be a very specialized solution.
Design experience makes the difference
Miller reached out to Bluco Senior Application Engineer, Todd Bennett, who told Miller something he was hoping to hear: Bluco had done this before. In fact, Bluco’s 30+ years of modular fixturing experience makes “we’ve done this before” a common theme no matter what the industry.
In the case of modular construction, Bluco had fixtured not only Z Mod’s Texas plant, but another modular construction facility located near Bluco in Naperville, Illinois. Miller made a visit to Bluco’s on-site Validation Center and to the modular construction facility nearby, where he was able to see similar solutions in action. “Seeing what Bluco had already done helped me visualize what was possible. From there, I started wondering how Bluco could take it to the next level,” says Miller.
A design curveball
With a taste of what could be accomplished using modular fixturing, Miller started assembling a wish list. While he originally wanted one fixture for roof assemblies, and another for floor assemblies, he challenged Bluco to take that idea and Make it Better.
“He asked us if we could design a single fixture that would hold both assemblies at the same time,” says Bennett. Working alongside Miller and his production team, the design started to take shape.
Results
Less floor space used
Reduced production cost
Faster throughput
Spot-on accuracy
Repeatability
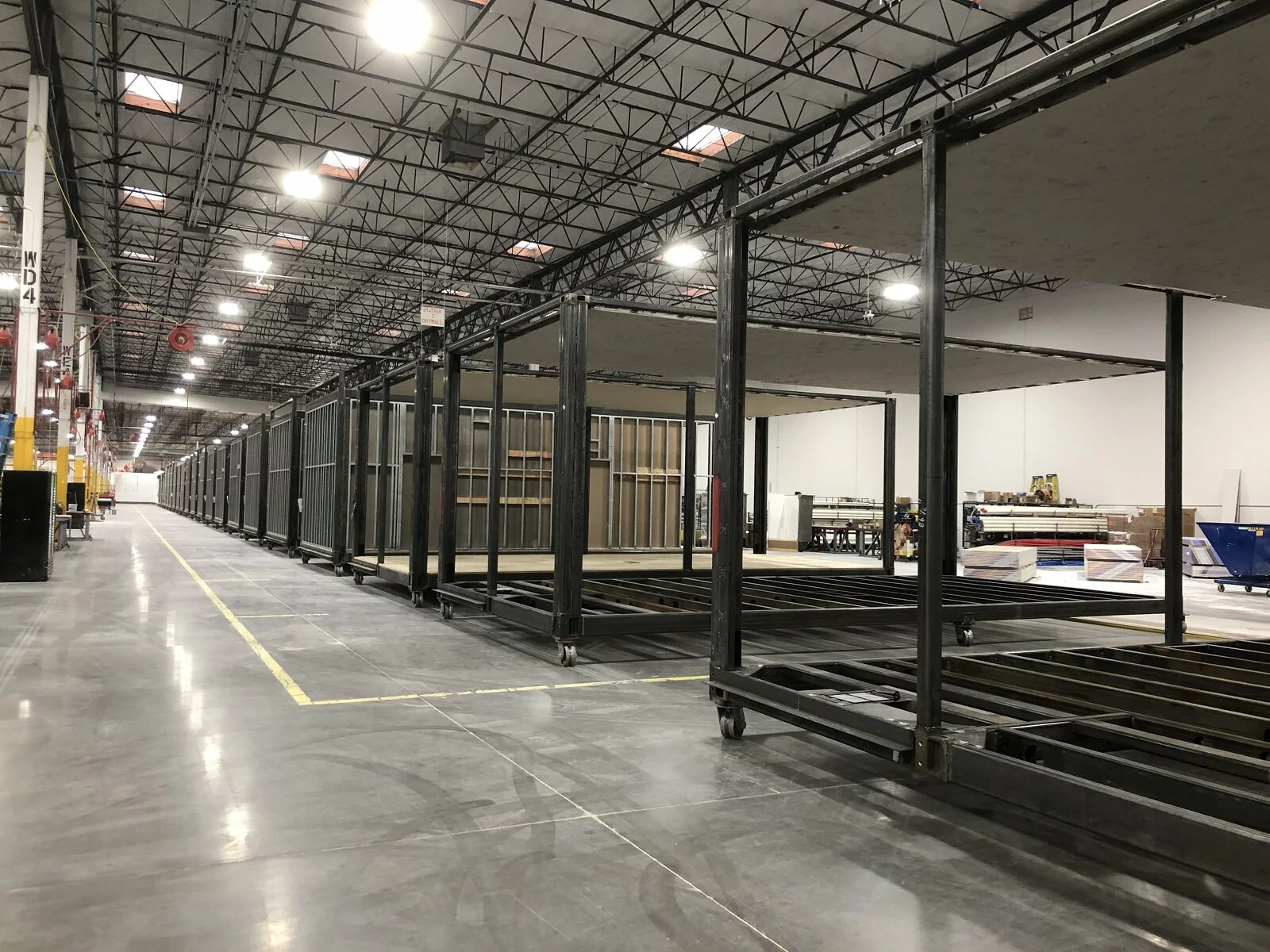
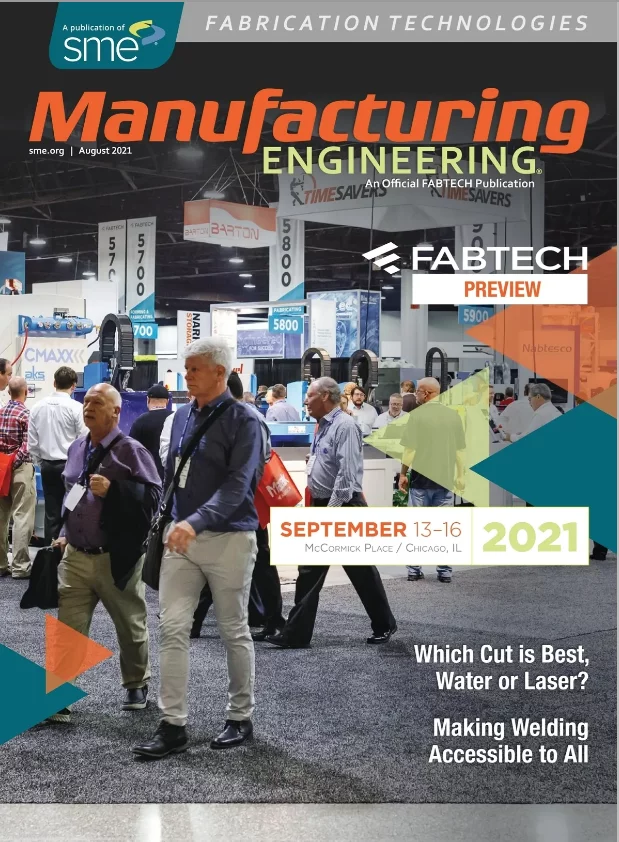
A home run solution in under two months
Ultimately, the solution would be a 60’ long floor rail system with 13 1/2’ vertical modular u-forms. From design to installation, the solution was up and running in 45 days. Getting there required a week of on-site installation (done by the Bluco team), out-of-the-box thinking, and an eye toward solving future challenges. “We weren’t just designing for what’s happening there this week, or even this year,” says Bennett. “We looked ahead to design for what happens when the automation comes online. Looking past that, how could we make it repeatable in other facilities.”
Double the production in less space
For Miller’s part, he’s now able to do two assemblies in the time it would have taken to do one under the original plan. This puts him one step ahead of the game. “Even when the automation comes online, we’ll still be using the Bluco system,” he says. “It will just help us build that many more.” On top of that, he’s saving space. “If we had gone with a fixed positioning system, we’d be really limited in our ability to move tooling around, and it would have taken up a lot more floor space,” he adds.
Looking ahead
Another goal of this project was to leave the team at Z Mod in a position to be able to handle additional fixture designs themselves. To that end, Bluco provided training on how to manipulate the modular components in CAD. But that’s hardly the end of Bluco’s involvement. “Even though everything worked exactly as we needed it to right from the beginning, we’re still looking at ways to make it better,” says Miller. “We’ve had multiple discussions along the lines of ‘yeah, we have it, and it’s working well, but is there an even better way to do it?’”
“That’s literally what Bluco is all about,” adds Bennett, “we won’t ever stop trying to Make it Better for our customers.”
< Have you seen this Case Study in Manufacturing Engineering Magazine? Check it out here.
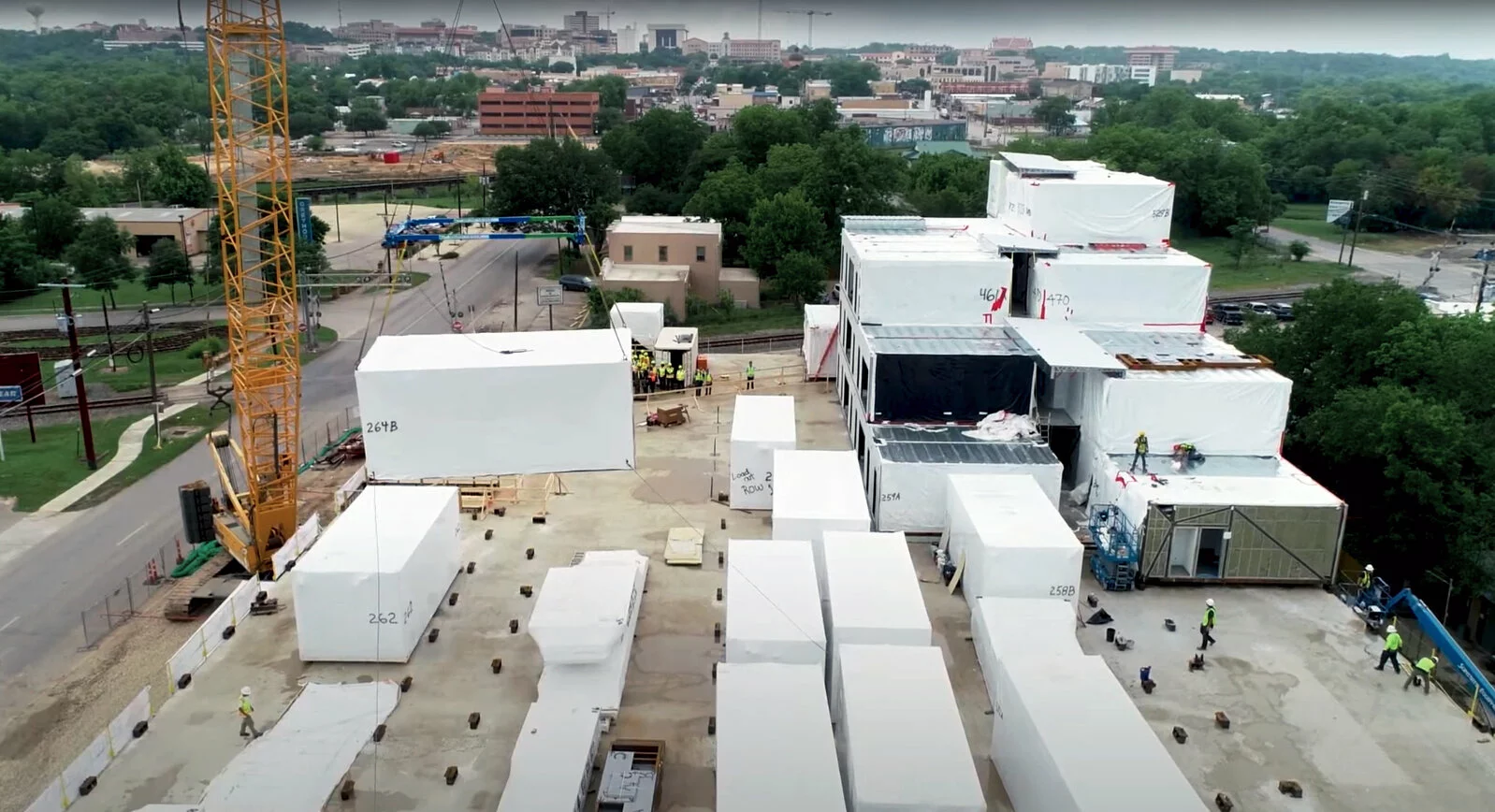
Modular fixturing delivers results for modular construction
Versatility
Productivity
Repeatability
“If we have anything were prototyping, we use the Bluco system, because it's easy for us to move things around. It's really for production but it comes in handy for those one-offs, too.” – Matt Miller
“Even when the automation comes online, we’ll still be using the Bluco system. It will just help us build that many more. If we had gone with a fixed positioning system, we’d be really limited in our ability to move tooling around, and it would have taken up a lot more floor space.” – Matt Miller
“We weren’t just designing for what’s happening there this week, or even this year. We looked ahead to design for what happens when the automation comes online…How could we make it repeatable in other facilities.” – Todd Bennett

Discover Bluprint™
Proposals only show how much it will cost. BluPrint proves how much you can gain.