Modular Welding Fixtures mean 2X Less Hands for Assembly
No modular welding fixtures turns out to be a no-go

Industry
Agriculture
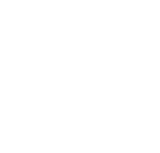
Challenge
Final Part Quality
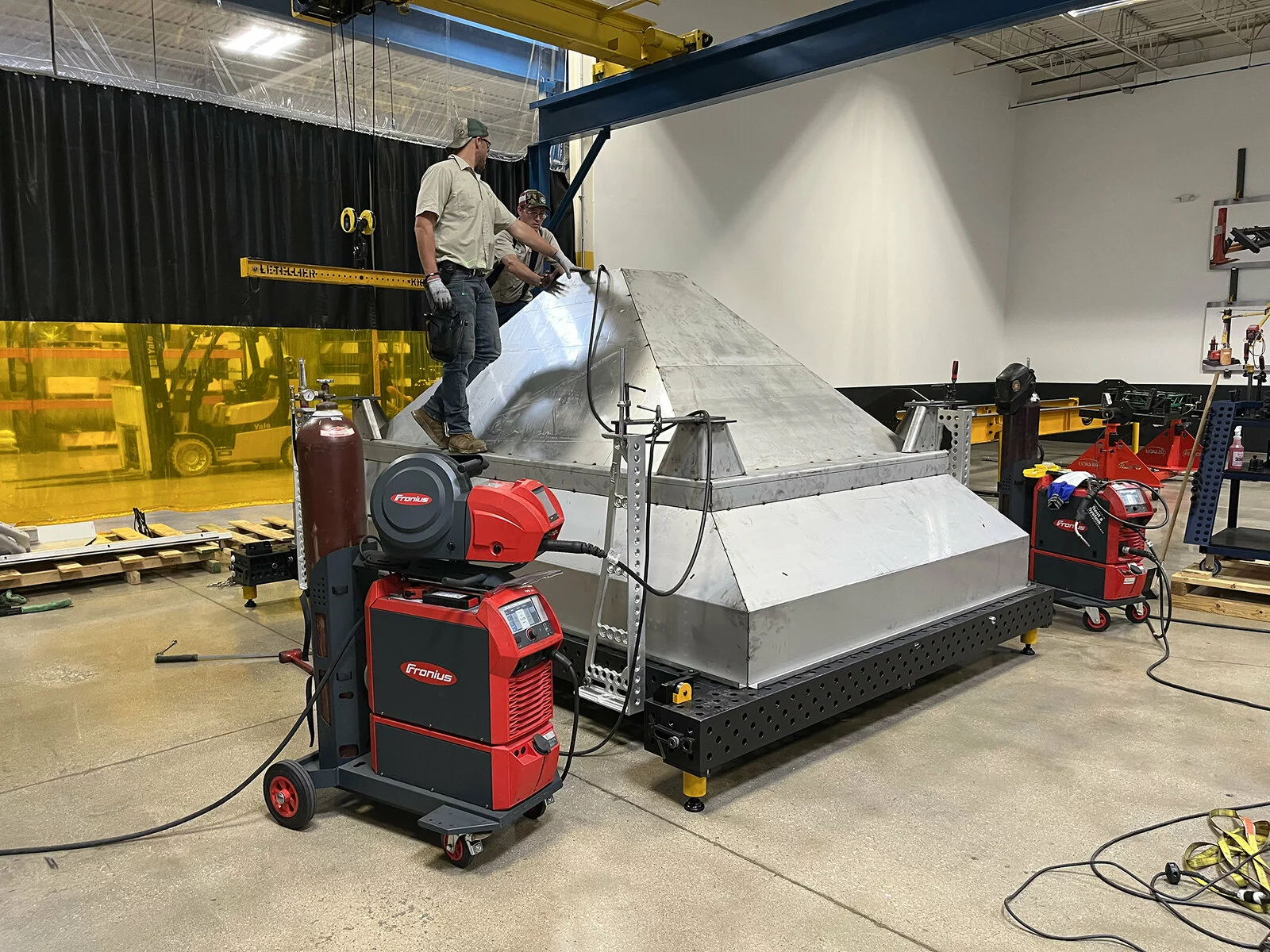
Challenges
Do what you’ve always done, and you’ll get the same thing you’ve always gotten. But “the same thing” was no longer good enough for this manufacturer of hoppers for fertilizer trailers. The team was building hoppers directly on the workshop floor. This approach tied up essential equipment like a crane and a forklift, and it required two workers — one of whom had to be a highly skilled fabricator — to ensure proper assembly. The result was a slow, difficult, and inconsistent production process. They were eager to upgrade, and reached out to Bluco to help them do it with a modular welding fixture.
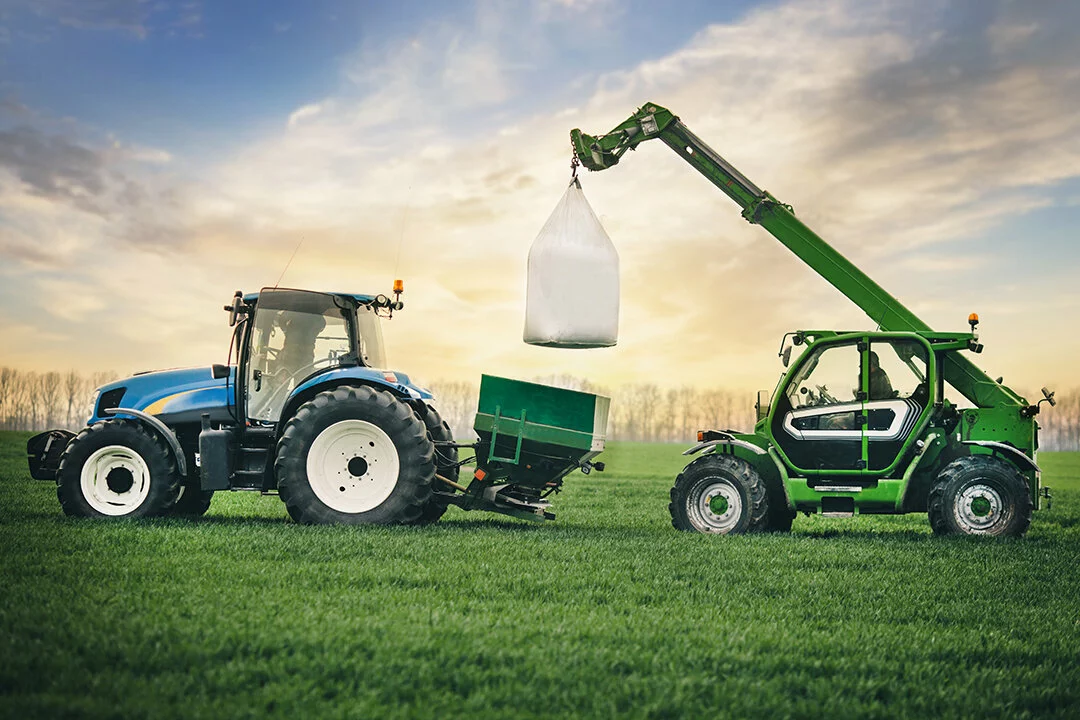
Bridging the Engineering Gap
While the rest of their production process was already optimized, the lack of a welding fixture made it easy to see that workholding was a major engineering gap. So Bluco engineers came up with a single versatile solution to bridge that gap and answer all the customer’s challenges. The design included a rolling base for easy repositioning anywhere in the shop. To ensure the angled hopper panels aligned perfectly at any pitch, custom plates were manufactured by Bluco. The vertical supports of the frame were made out of lightweight aluminum for quicker set-up and changeover that no longer required a crane. And as an added perk, the new modular welding fixture also accommodated leg assemblies.
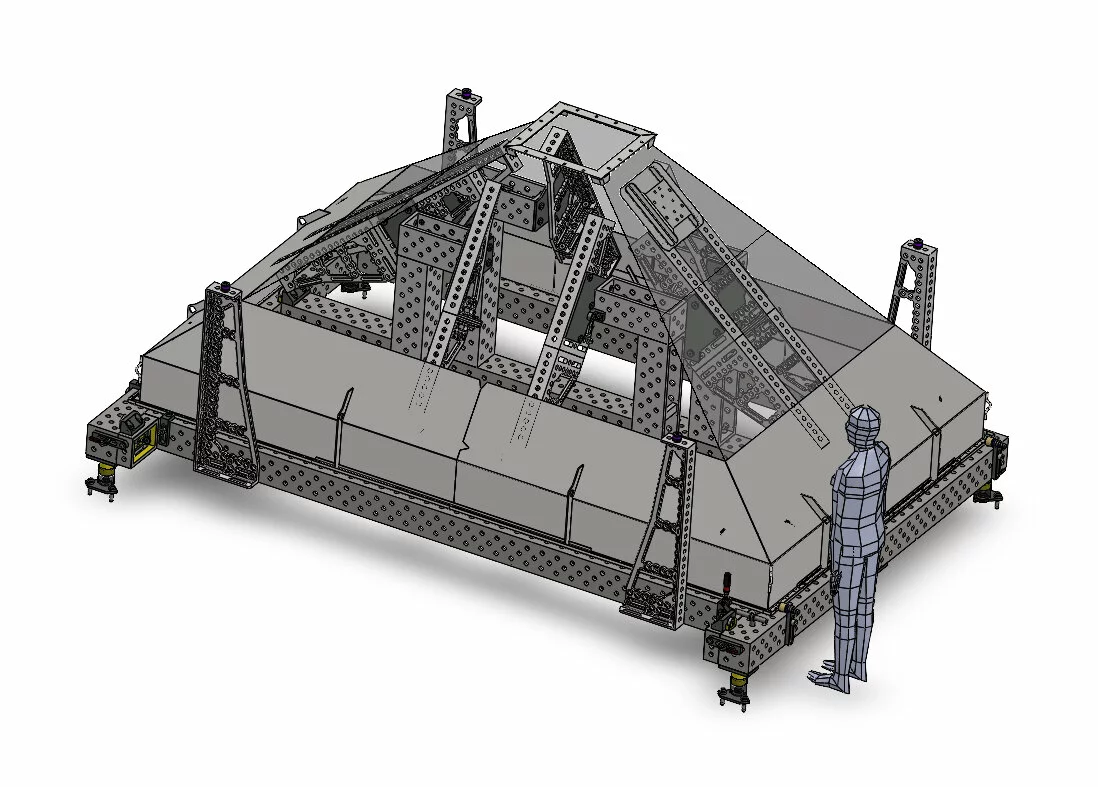
Projected X-Factor Improvement
The outcome was an immediate improvement across the board. The new modular fixturing ensures that each hopper is made consistently and to spec. What’s more, the entire assembly can now be managed by just one person — and that person no longer has to be an experienced fabricator. This puts senior staff back where they’re needed most and also frees up the crane and forklift for other tasks, making the whole operation more efficient. The success of the welding fixture led the team to purchase another modular solution, and additional cells are under review. Overall, the company’s investment in moving beyond the status quo has exceeded their expectations and helped them level up their entire operation.
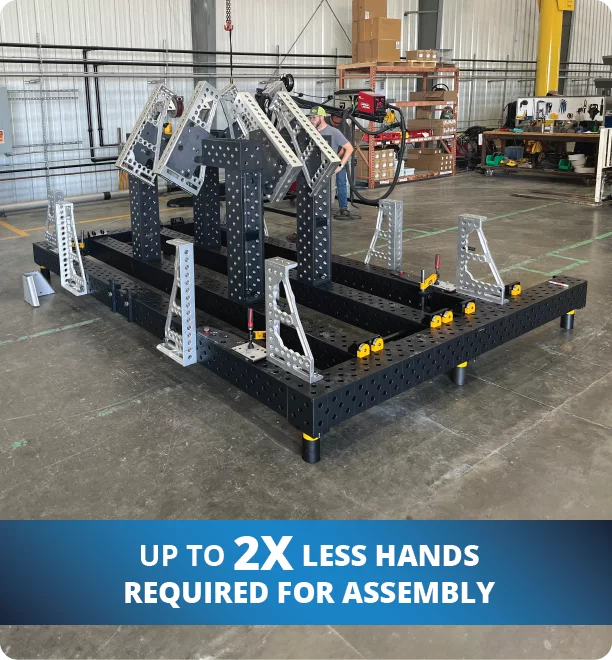

Discover Bluprint™
Proposals only show how much it will cost. BluPrint proves how much you can gain.