Modular Fixture - More Accuracy, Less Work, No Tape Measure
Safer, faster, and more accurate food processor production with modular fixturing
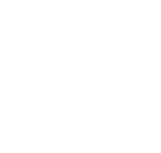
Industry
Industrial Equipment
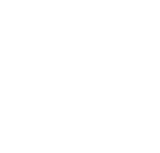
Challenge
Accuracy
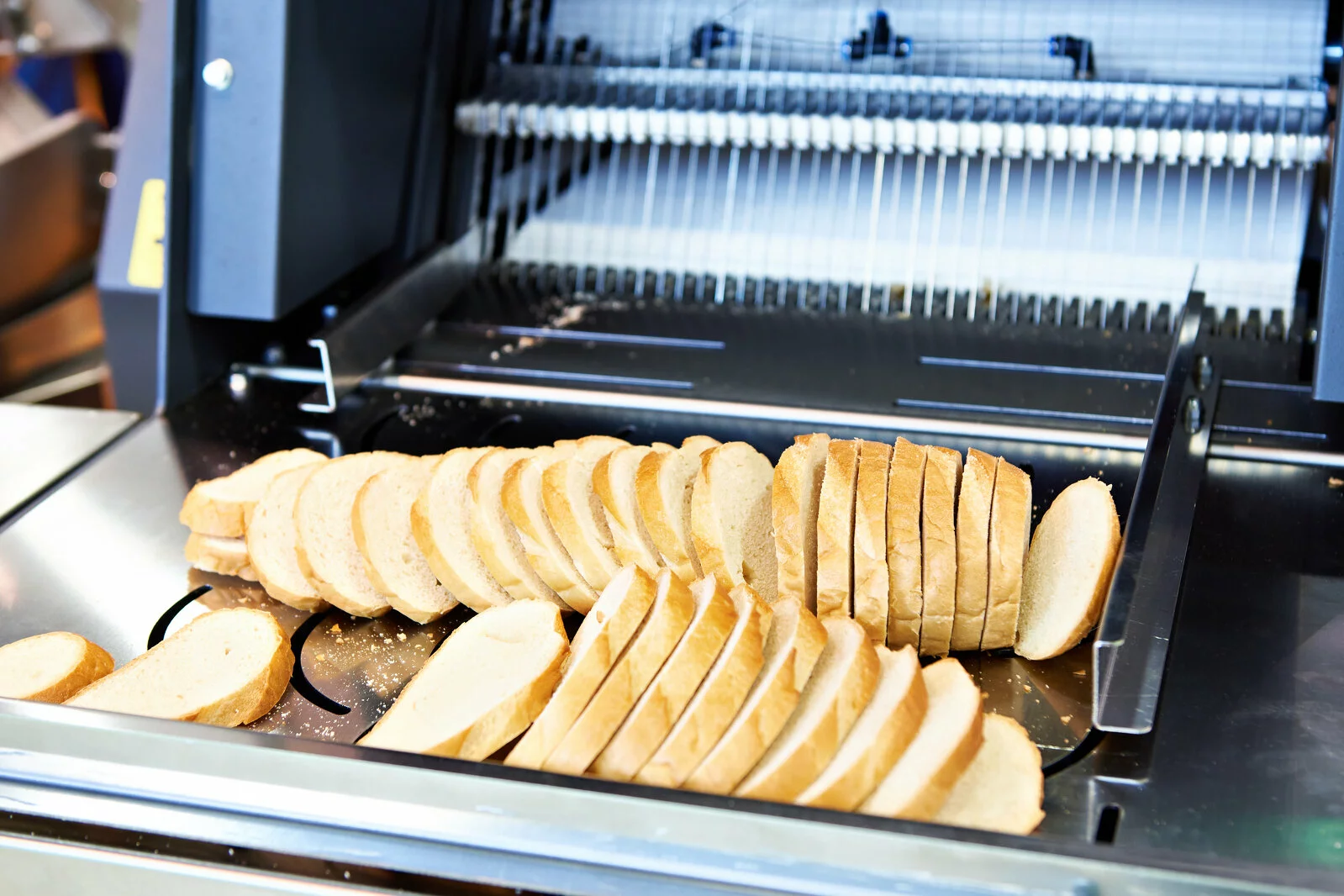
Challenges
Measurements for these industrial food processors need to be spot on, or the internal conveyors won’t run smoothly. But welders were spending too much time measuring each weld with a tape measure and laying them out by hand. Any overlooked measurements introduced inconsistencies that meant rework and delays.
In addition, after technicians tacked the frame in place, they had to manually flip it over on the floor to position it for welding. Not only was it dangerous to move these large and heavy parts, it was also uncomfortable and time-consuming for welders. It created a workflow that was not only inefficient, but physically taxing. All reasons why a modular fixture on a Multi-Axis Positioner was the perfect fit for this manufacturer.
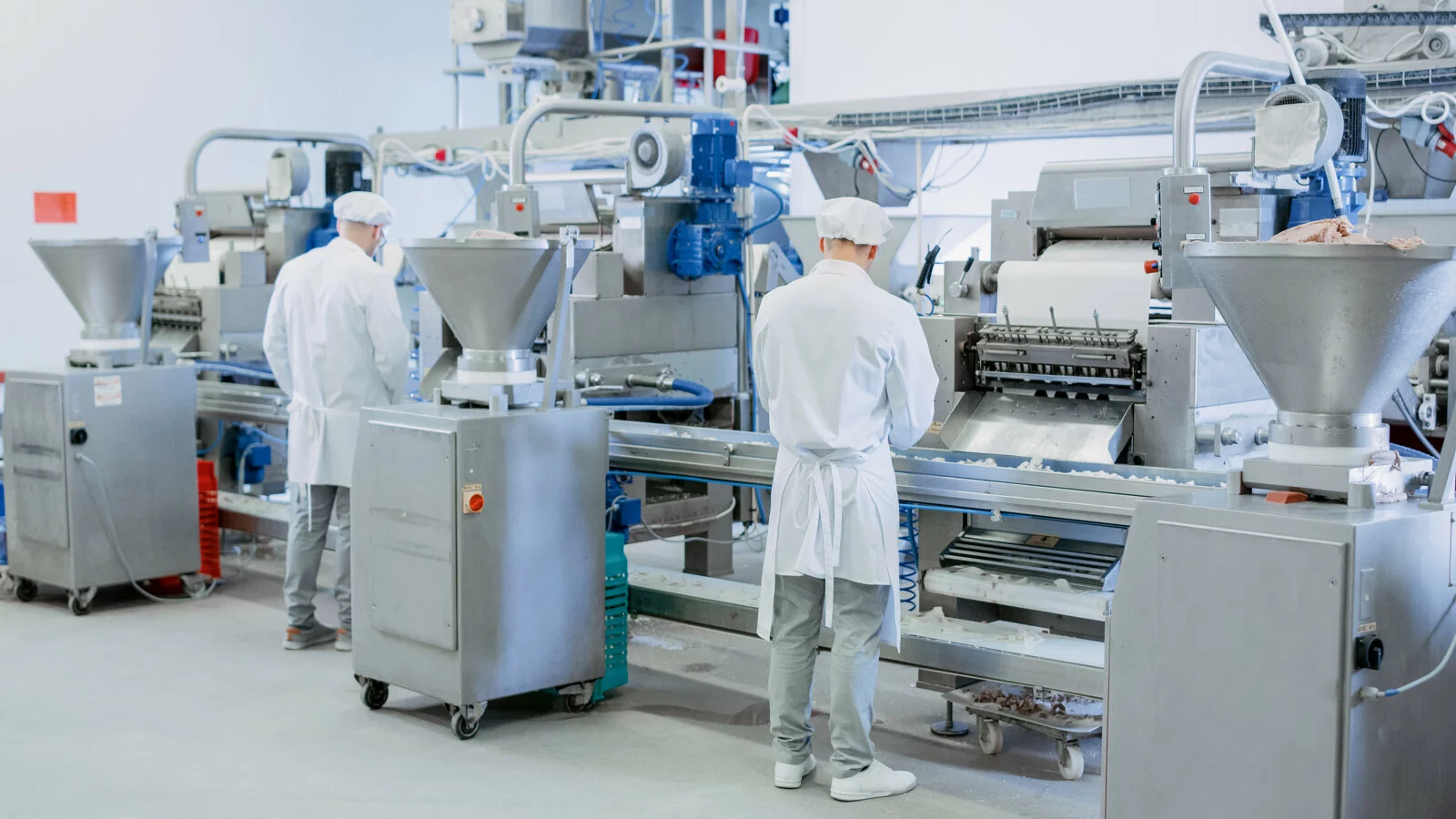
Solution
• Multi-Axis Positioner
• Tooling package
Our expert engineers collaborated with this manufacturer to create the best modular solution for their needs: a M2000 Multi-Axis Positioner equipped with modular fixturing to hold parts in place with extreme accuracy. Technicians need to load the parts only once to complete all welds. The positioner allows for push-button control of lift, tilt and rotate functions. The ability to access every weld without manually flipping the part makes a dramatic difference in both speed and safety.
Speaking of expert engineers, did you know ours offer Engineering Design Services? Read more here.
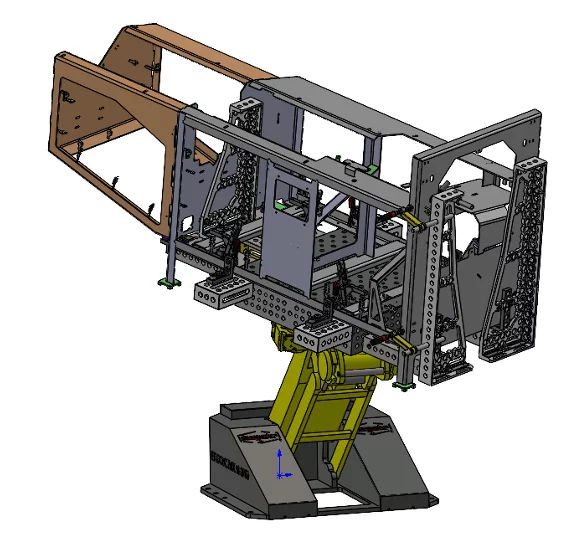
Result
This approach delivers repeatable accuracy in half the time and requires much less rework. Modular fixturing allows parts to be loaded quickly, and the precision hole pattern and compatibility of components and tables means tape measures and hand layout are no longer necessary to achieve welds that keep the conveyor running smoothly.
Welders can instead focus on quality execution, knowing that the modular fixturing guarantees alignment and accuracy. Even better, they no longer have to flip cumbersome frames on the floor between welds. Safer, faster, and more accurate. Problem solved.
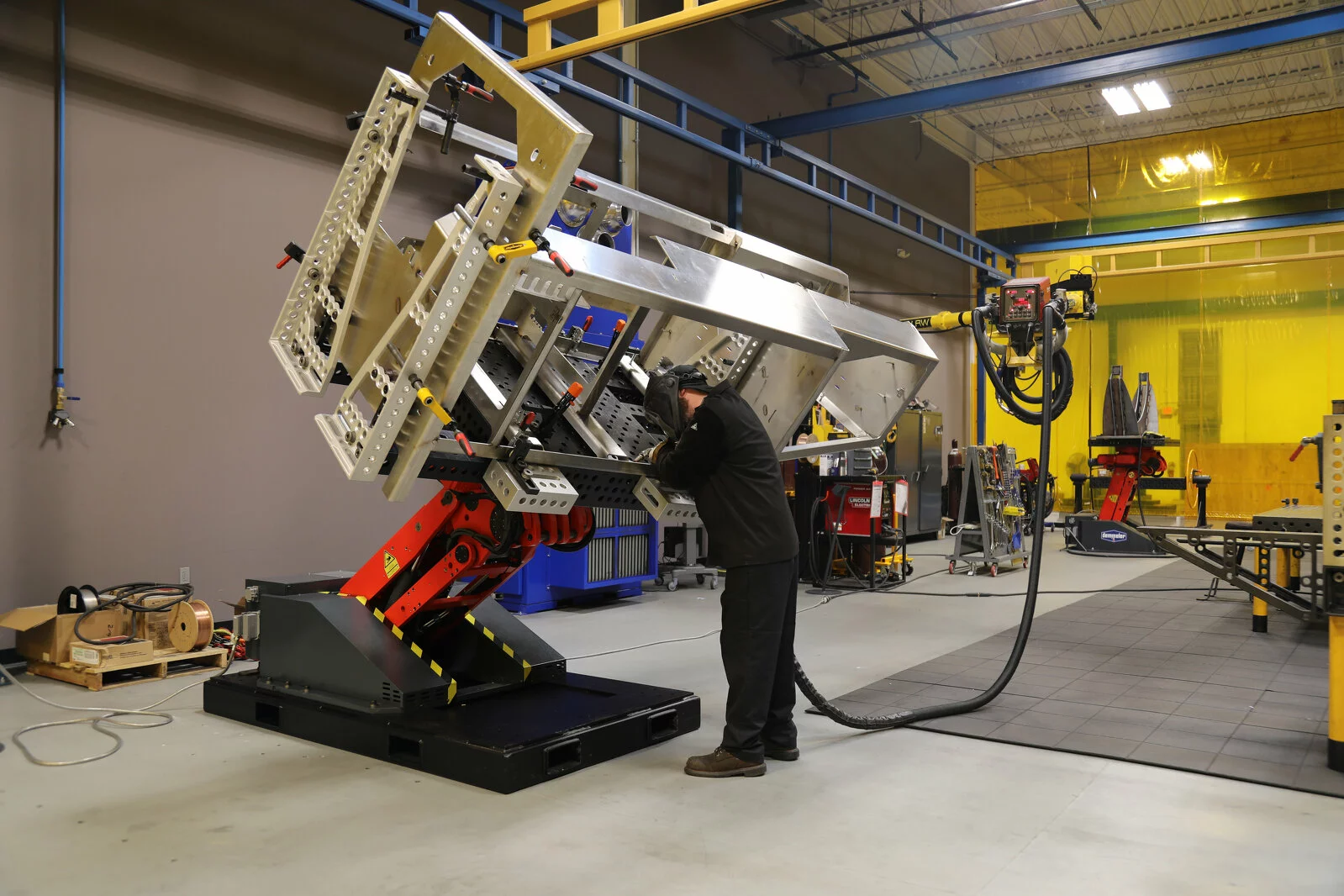

Discover Bluprint™
Proposals only show how much it will cost. BluPrint proves how much you can gain.